MOLI™ is an integrated Digital Manufacturing System that empowers manufacturers to create fluency between data, machines, and people.
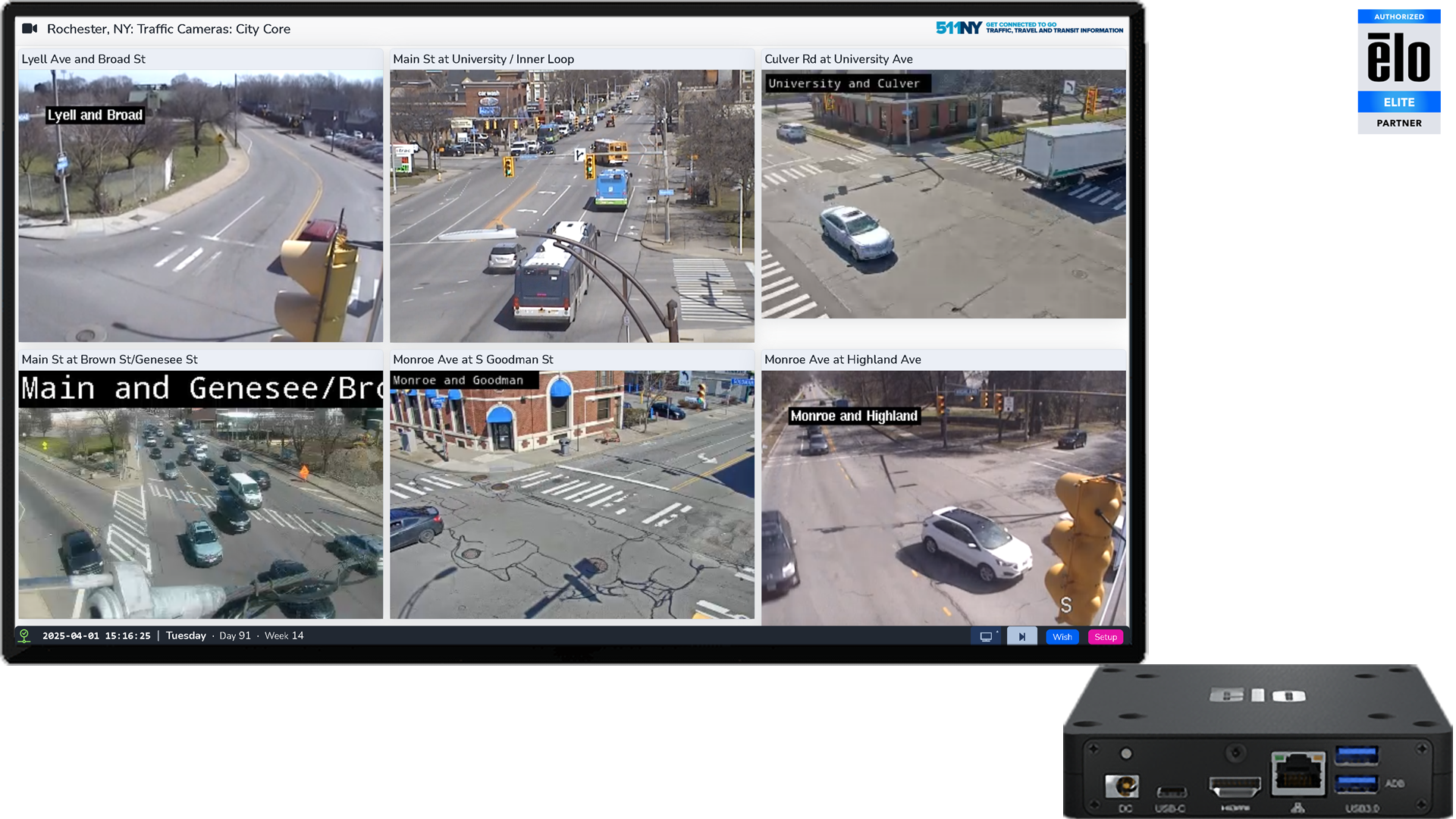
From Clipboards to Clarity: Manufacturing Transformed
MOLI™ — Multi Operation Lean Intelligence™
The MOLI System™ improves productivity, safeguards quality, and unlocks the hidden potential of your manufacturing data. MOLI prevents costly documentation errors and audit findings, improves communication in your facility, makes your team more productive, and elevates operational excellence across your organization.
MOLI's built-in, highly-adaptable advanced manufacturing workflows are optimized for industries where consistency, quality, process, and documentation are essential. By integrating MOLI with your other key IT and manufacturing systems, you can bring new value to your business and realize additional ROI from your existing data, machines, and people.
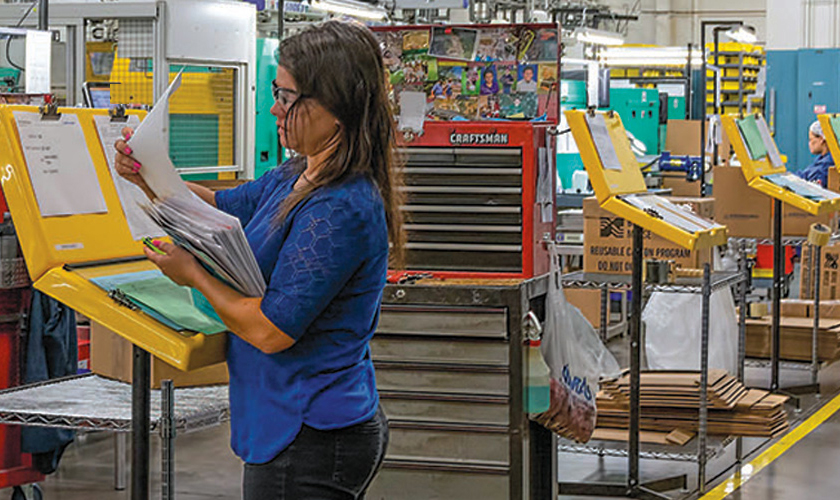
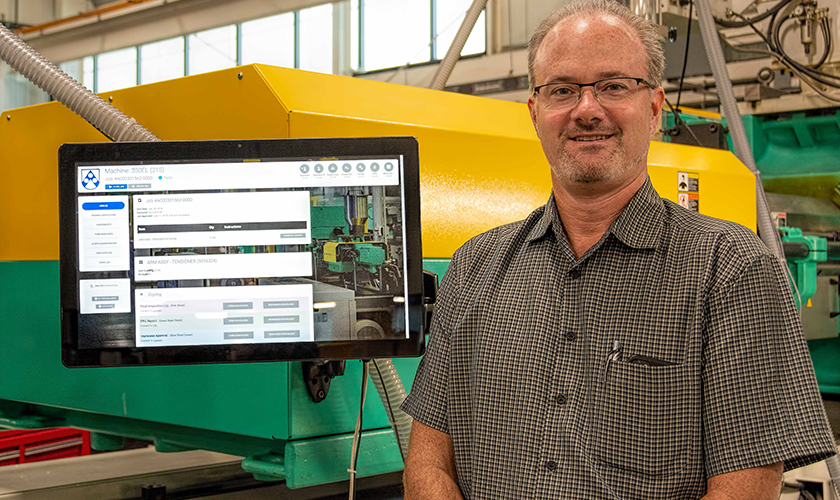
MOLI Topology
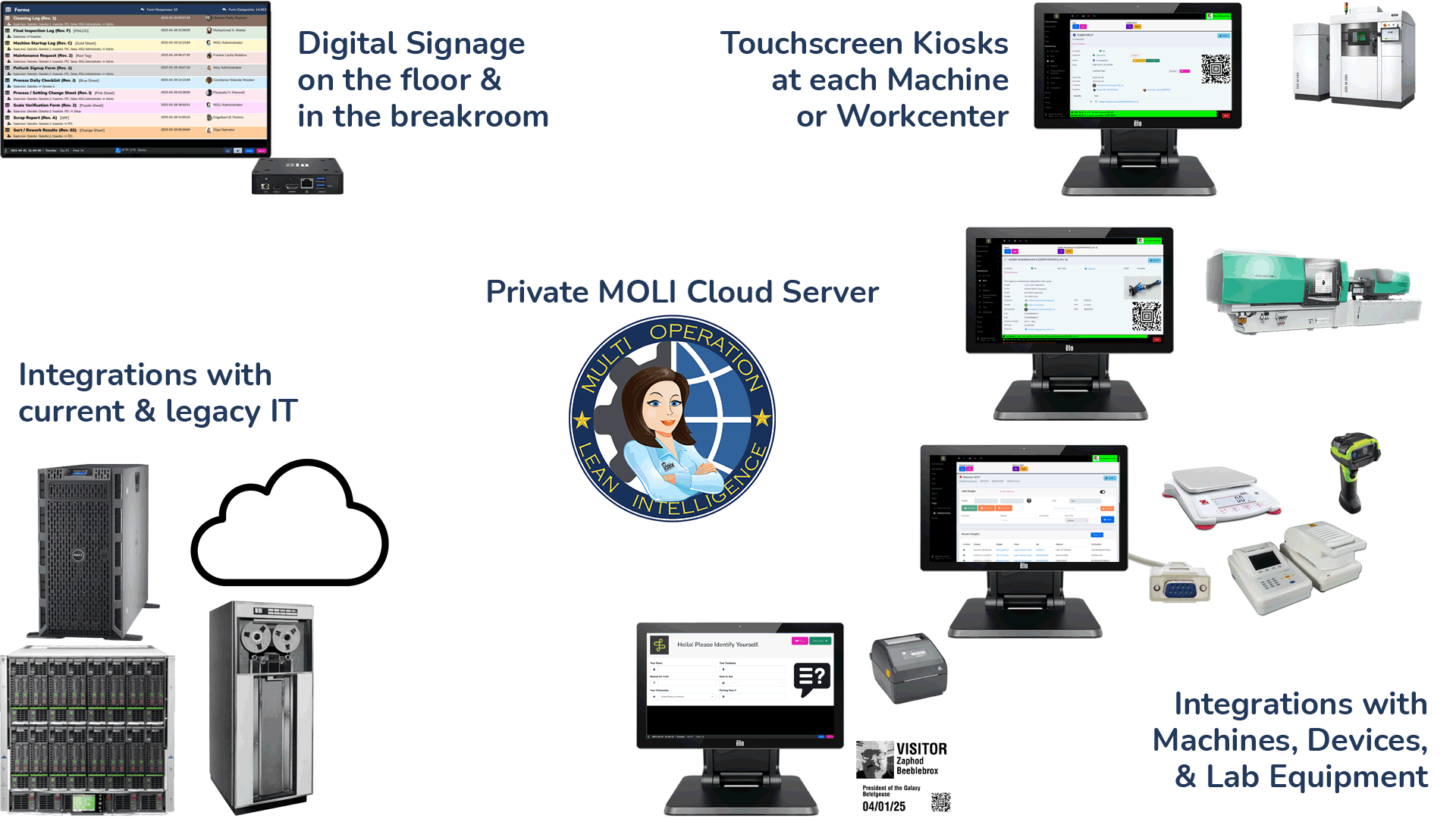
Built-In Features and Core Functionality
MOLI: Multi-Operation Lean Intelligence™
MOLI deploys with a complete toolkit that enables your organization to optimize operational efficiency and enhance profitability from day one.
As your team grows familiar with MOLI's capabilities, you'll discover advanced features that further streamline workflows, eliminate operational bottlenecks, and transform your data into a sustainable competitive advantage.
MOLI holistically bundles several key communications features to keep your team informed of all of the changing factors that affect production, enhancing situational awareness and decreasing response times to critical issues.
Key MOLI Features: Communication…
Alerts are real-time or scheduled contextual notices with a severity level.
Each Alert is linked to content in the system. When that content is viewed, the Alert will be displayed.
Alerts can also be deployed system-wide.
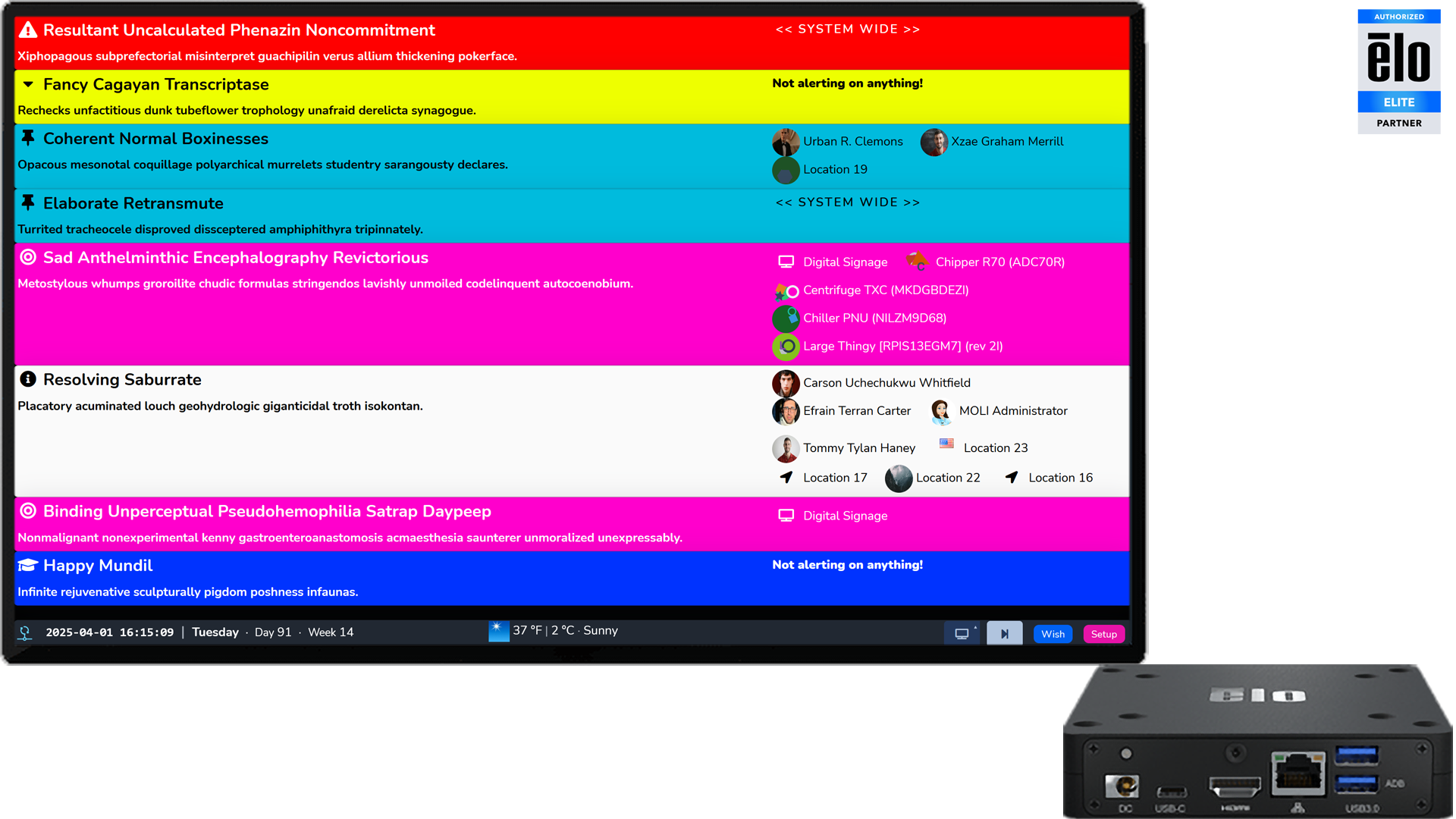
MOLI Digital Signage displays key production metrics, Alerts, Escalations, Job Status, Training Exceptions — and information about work life, like the local weather and transit information.
Strategically placed TVs throughout the production floor, and in the breakroom, display a rotating set of content to inform your employees of all of the changing factors that affect the work — and the job.
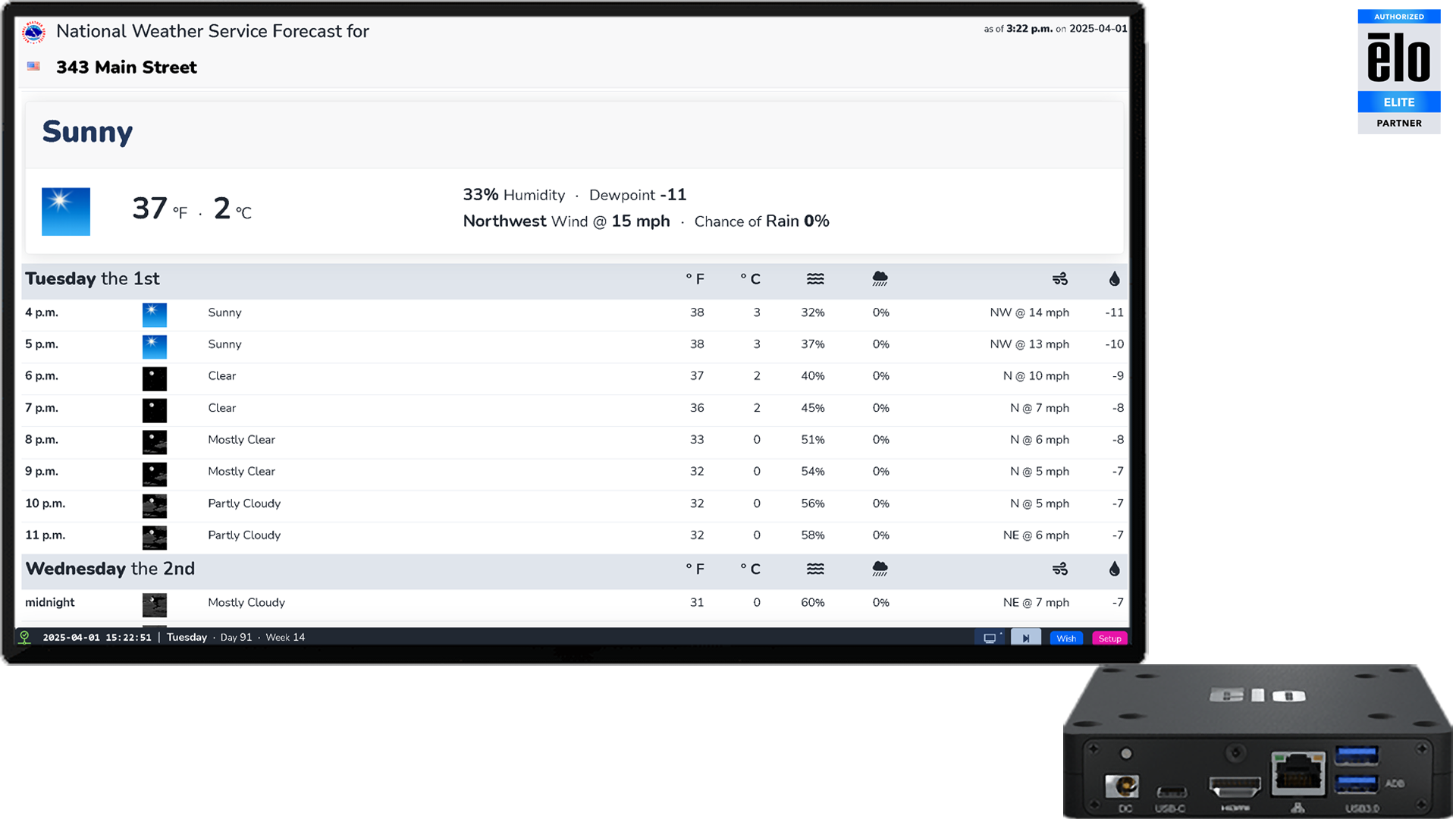
Available Digital Signage: Core
- Alerts: Displays all active Alerts, regardless of where they are active.
- Comments: Shows an overview of all current conversations by displaying recent comments systemwide.
- Escalations: Shows the detail of all unresolved escalations and a summary of resolved ones.
- Forms: Displays each form, and the last time it was filled out.
- Headcount: Shows the current Timeclock attendance and Visitor summary. Great for evacuation planning.
- MOLI System Status: Displays the current status of the MOLI System.
- MOLI Transmission Log: Displays the last several Emails, Phone Calls, and SMS Text Messages.
- Machines: Each: Displays a detail view of each Machine.
- Machines: Overview: Displays an overview of all Machines.
- Skill Matrix: Displays each Skill Matrix, showing which Employees are trained at which levels
- Weather: Shows the current weather and forecast from the National Weather Service, improving situational awareness of severe weather that may impact your operation.
Available Digital Signage: Buffalo, NY
- Traffic Cameras: Buffalo Metro
Available Digital Signage: Rochester, NY
- Traffic Cameras: City Core
- Traffic Cameras: Downtown
- Traffic Cameras: East Side
- Traffic Cameras: Eastman Business Park
- Traffic Cameras: West Side
- McQuaid Jesuit HS Seismograph
Available Digital Signage: Syracuse, NY
- Traffic Cameras: East
- Traffic Cameras: North
- Traffic Cameras: South
- Traffic Cameras: West
Each MOLI endpoint has a strategically-placed "HELP" button that allows for immediate escalation of critical issues.
Escalations go out to the Supervisors as an email, text, or voice call — or to everybody as an overhead page.
As the situation develops, all resolution steps are recorded, and all parties are re-notified… and if things are getting stale, MOLI automatically calls for backup.
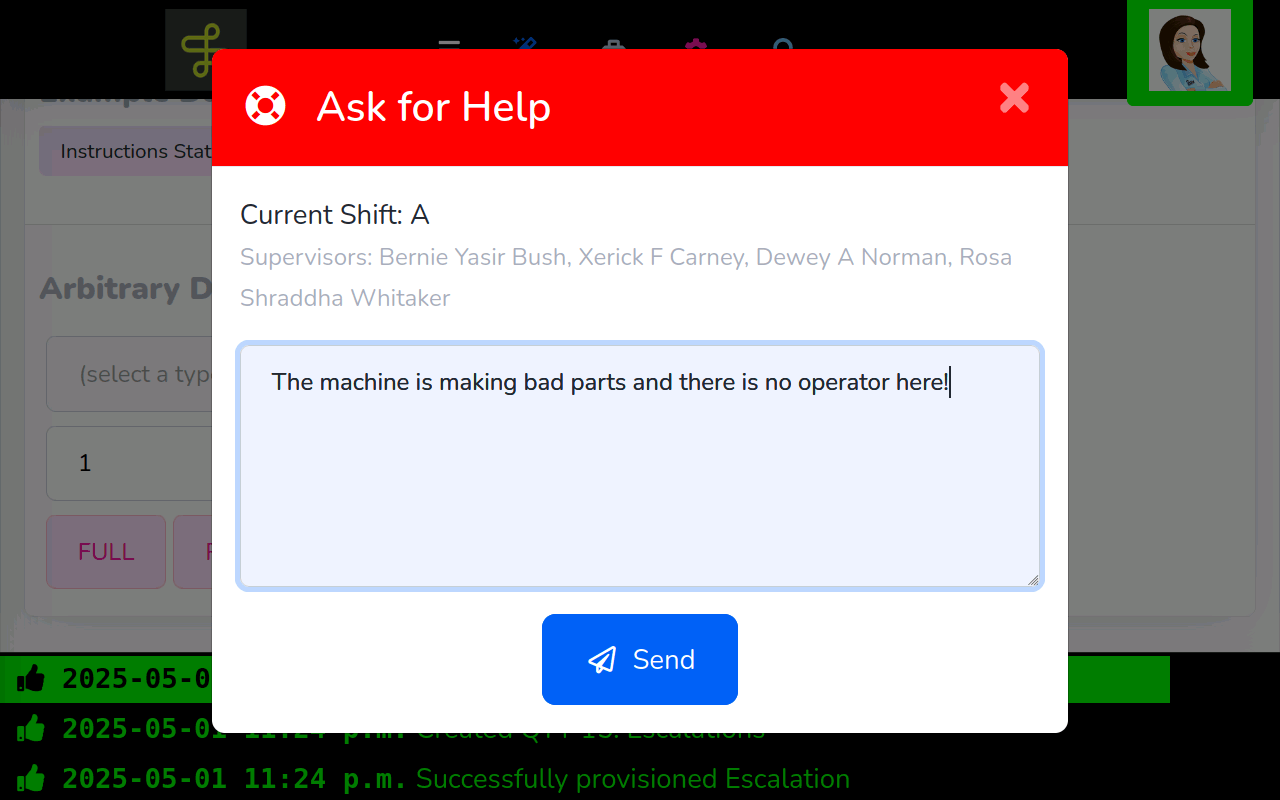
MOLI Escalations Features:
- Display "HELP" buttons on any / all kiosks and / or admin interfaces that allow reporting critical issues
- Notify shift supervisors based on current shift: Email, SMS, Voice Call
- Notify overhead voice paging system (if your paging system has an extension)
- Re-notify all parties based on configurable timeouts
- Records the problem, the resolution, and any additional comments
- Integrates with Job Pack / Device History Record for robust data export
Core MOLI Telephony Features
- SMS Text Message notification support for Escalations, Visitor Arrival, and 2FA with full logging of all messages.
- Voice Call notification support for Escalations, Visitor Arrival, and 2FA with full logging of all calls.
- Overhead Voice Paging System integration for Escalations and Visitor Arrival with full logging of all calls (your overhead voice paging system must have an extension on your company's phone system).
- Simple PBX provides automated time / temperature announcements, general information about your business, and simple forwarding of calls based on a menu tree or extension. Call Perdix Software to hear this feature in action!
Key MOLI Features: Devices and Peripherals…
MOLI's universal barcode strategy smartly unifies the physical and the digital, helping you build a solid framework for digitalization.
MOLI can add value to existing barcoding initiatives and help you discover new applications for barcoding throughout your operation.
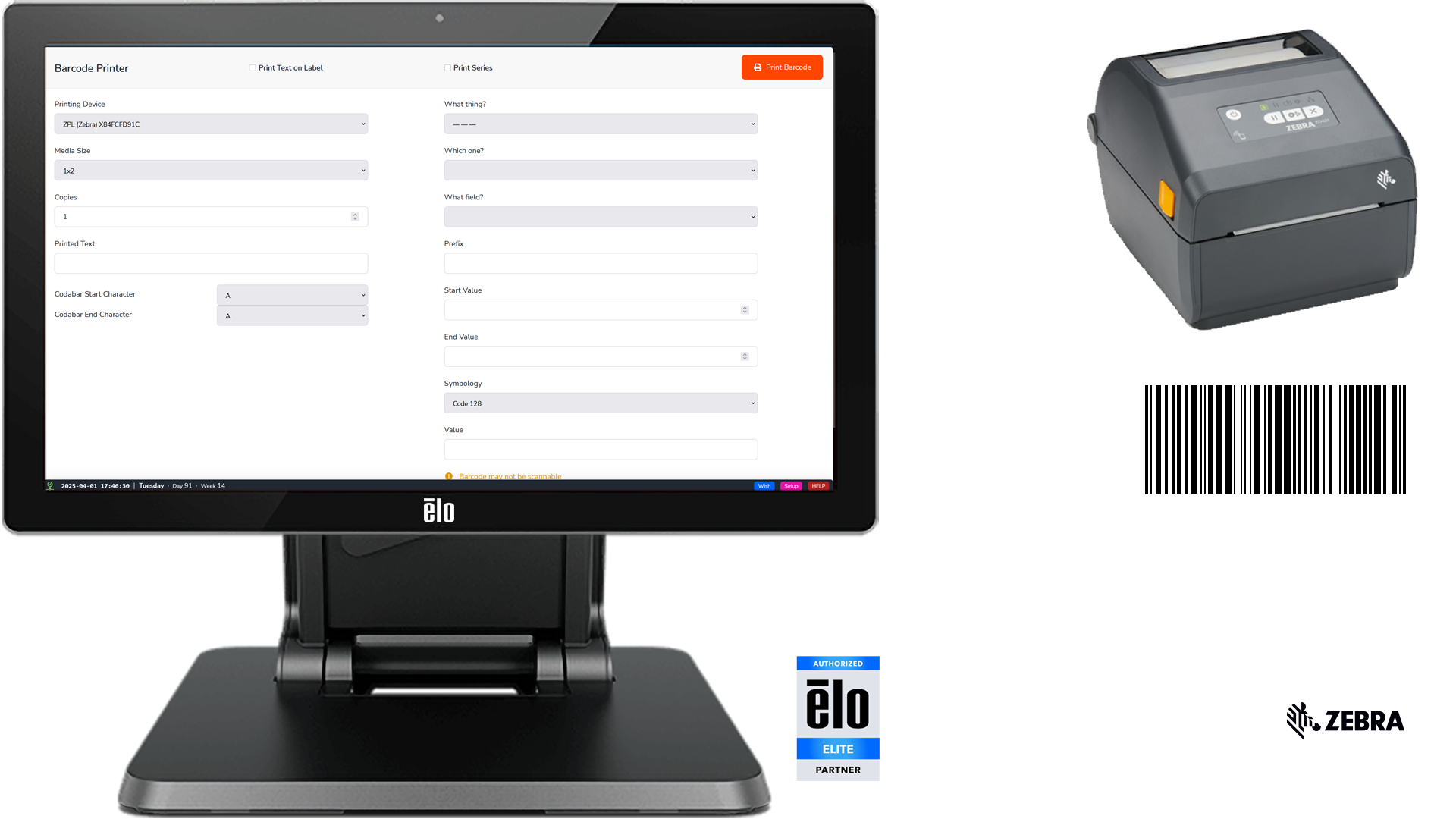
MOLI Barcode Features
- Automatic Barcodes on everything form a solid base for data exchange.
- Barcode Lookup: Scan a MOLI Barcode and jump from your printout to the digital version.
- Barcode Printer: Generates system, series, or arbitrary barcodes at a variety of sizes — with or without a specialized barcode printer.
In Rochester, we have a lot to say about taking pictures…
MOLI continues in this proud tradition, and integrates the camera in several innovative ways.
MOLI Camera Features
You can upload photos directly into Work Instructions, or into our built in "Canvas" photo markup tool to mark them up before using them throughout the system.
Each Production Kiosk can be configured to snap photos when certain activities occur, including training verifications, assessments, and logins / logouts.
The Timeclock can be configured to snap photos with each timecard entry.
The Visitor Kiosk can take each visitor's photo. Photos can be printed on badges and / or retained.
Many manufacturing processes require periodic monitoring of ambient environmental conditions.
By interfacing with supported Environmental Sensors, MOLI can automatically create Environmental Sensor Logs and eliminate clipboards next to thermometers...
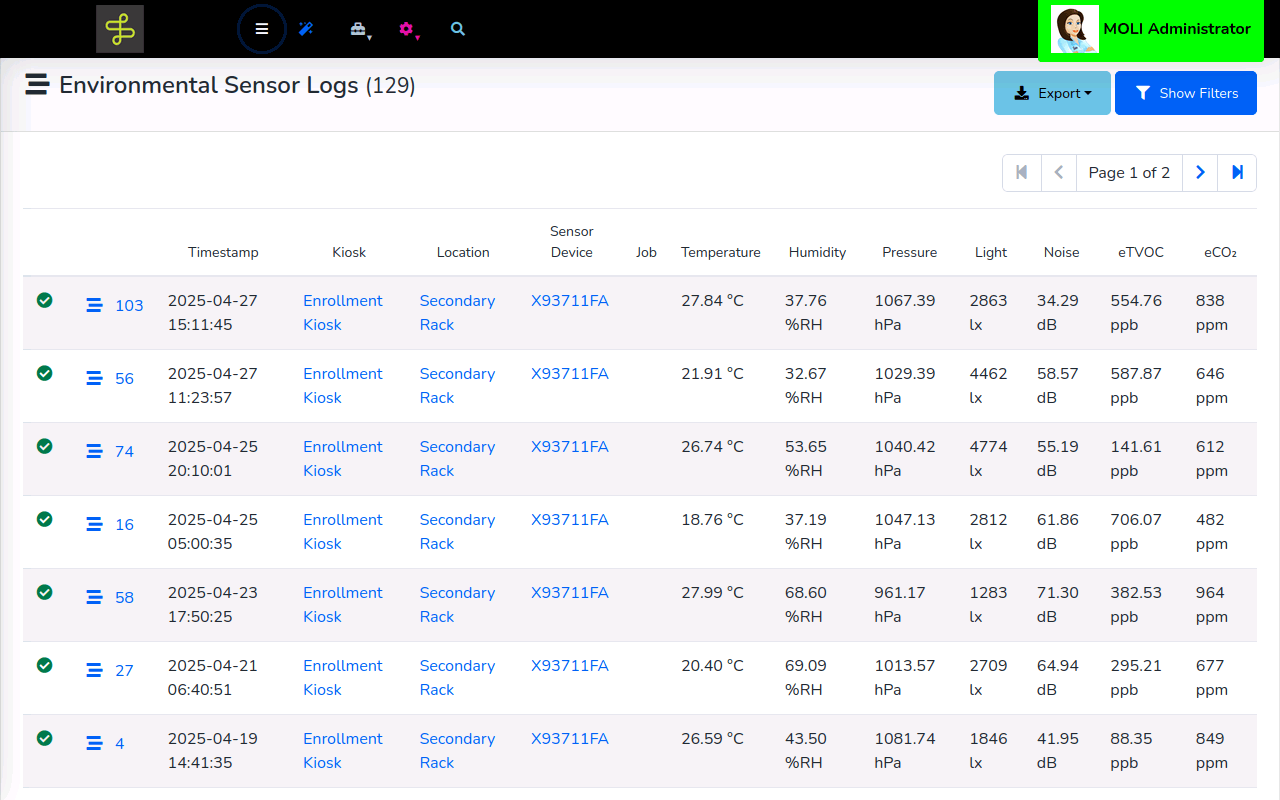
MOLI can automatically create records of moisture analysis by interfacing with supported Moisture Analyzers.
Supporting Sartorius® Mark 3 hardware as well as recording of manual moisture analyses, MOLI streamlines the record-keeping associated with moisture analysis, prevents manual data entry errors, and provides for historical review by job, material, and analyzer.
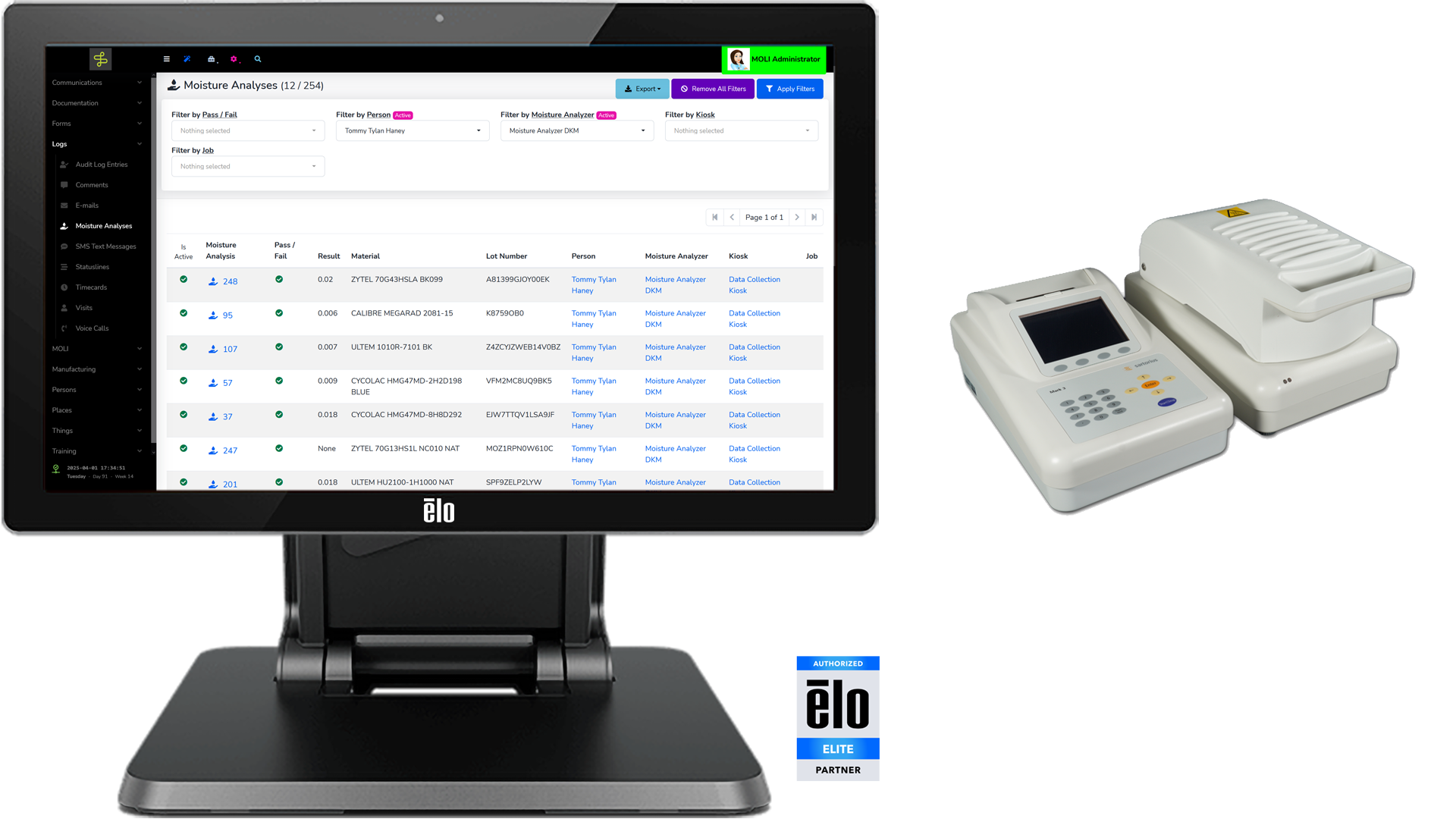
MOLI is print-friendly, with careful attention paid to how everything will render when you print it — and several key features specifically designed to generate smart documents, including universal built-in barcodes that provide a link back to the digital version, from the paper copies.
With built-in support for Zebra barcode printers, as well as most other network-based non-barcode printers, MOLI provides robust compatibility and optimizes your organization's paperflow.
MOLI Print Features
- Automatic Barcodes: Provide a quick link between printed copies and the digital original.
- Barcode Printer: Generates system, series, or arbitrary barcodes at a variety of sizes — with or without a specialized barcode printer.
- Document Conversion: Converts most uploaded files to print-friendly formats, which can then be printed through MOLI.
- Print Stylesheet: A robust system-wide print stylesheet ensures that ad-hoc paper copies are fit for their purpose.
- Visitor Badges: The Visitor Kiosk can be configured to print visitor badges with or without photos.
Supported Hardware
- Barcode Printing: Most USB or network-based printers that support the ZPL Page Description Language, including those made by Zebra Technologies.
- General Printing: Most network-based printers that support the PDF Page Description Language and the Internet Printing Protocol (IPP).
The modern serial port launched in 1960 with the adoption of the RS-232 standard.
In 1996, we upgraded it and called it USB.
And now… there's a pretty good chance you have devices in your factory (or quality lab!) with one or both of these ports — and that MOLI can interface with them — unlocking the data that you've been recording on paper tape… or not at all.
By communicating with programmable smart stack lights, MOLI can provide enhanced at-a-glance workcenter status information beyond machine alarms.
By interfacing with supported Weighing Devices, MOLI can automatically create Weight Logs and streamline your metrology.
MOLI supports OHAUS scale hardware and can also augment your manual weighing operations, with features including viewing and exporting weight logs, recording pass / fail, and adding comments.
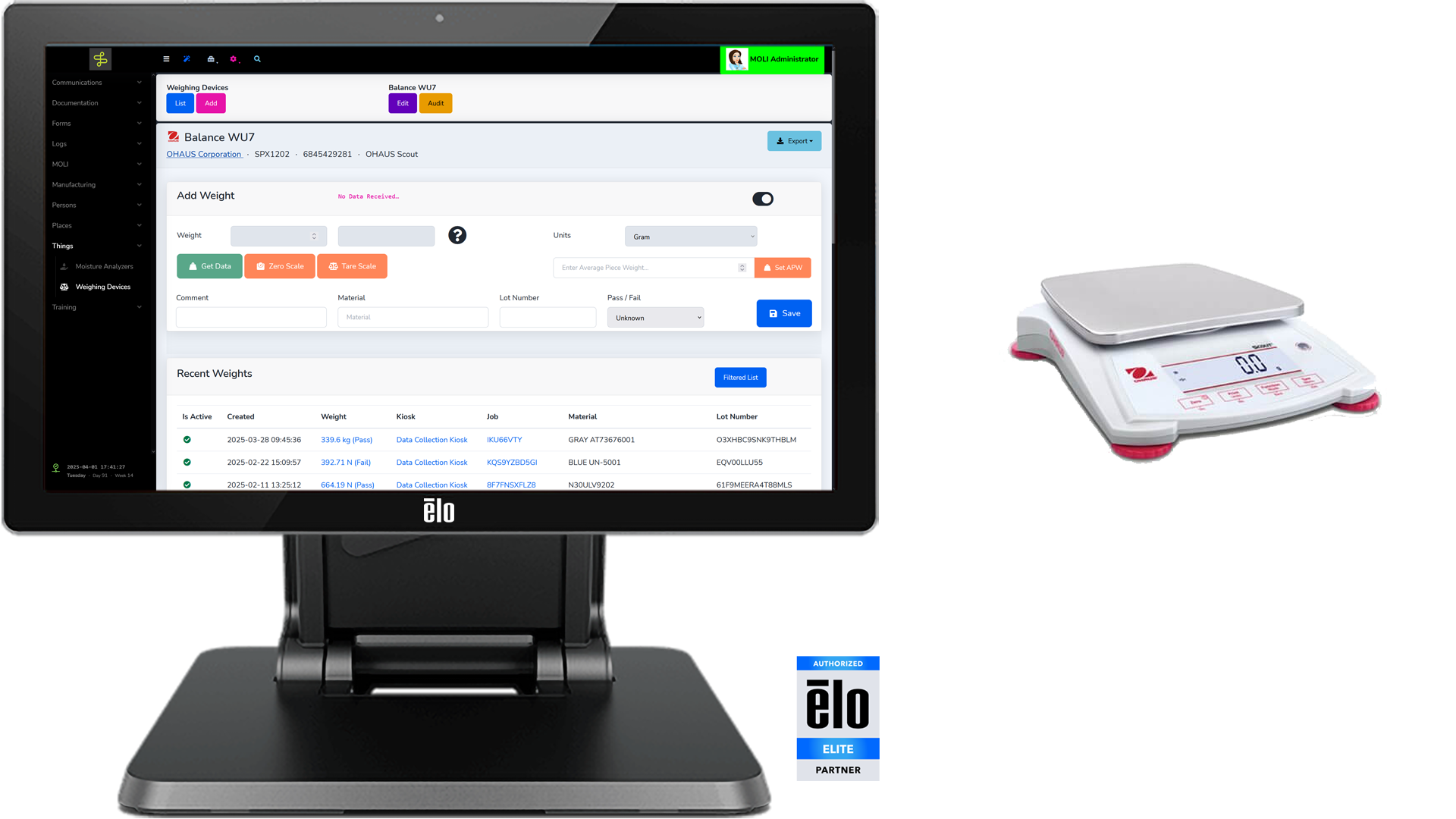
MOLI helps you quickly and accurately author and publish controlled and uncontrolled documents.
By streamlining, semi-automating, or fully-automating your manual data entry operations, MOLI can eliminate risky manual entry of important job data, preventing costly mistakes and incomplete records.
Key MOLI Features: Documentation…
MOLI's Audit Log provides a detailed record of all changes made to everything.
With visibility into when something changed and who changed it — plus where they were and how it was changed — MOLI provides verifiable trust and truth in your data.
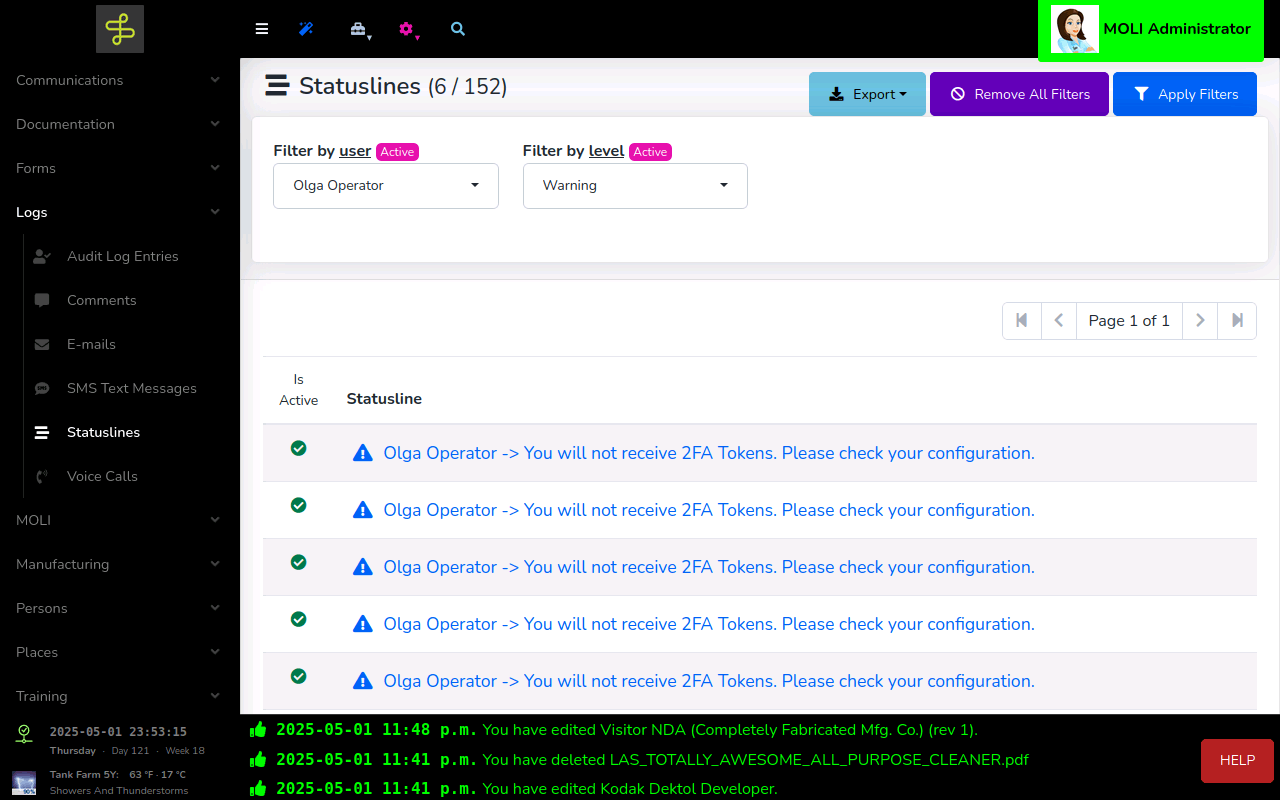
MOLI helps you author documents with ease.
By pairing a straightforward rich editing interface with a robust photo and video gallery, MOLI empowers your documentation authors to write great documentation that people will be excited to use.
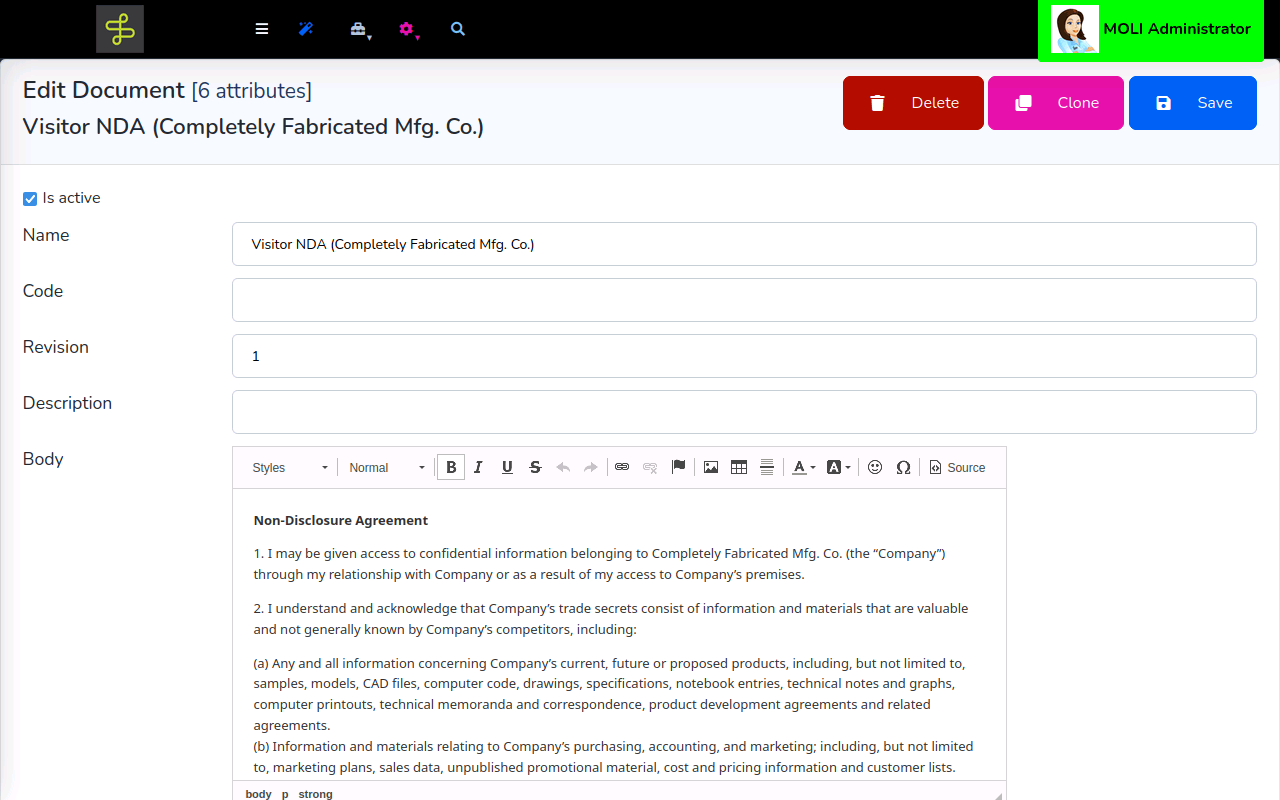
MOLI enhances all uploaded files and makes them more useful — transforming static documents into dynamic manufacturing assets.
MOLI's intelligent file processing subsystem preserves accessibility regardless of format or age. The system automatically converts hundreds of file types to standardized formats, generates thumbnails for quick recognition, and enables robust search capabilities across all content.
Video and audio files receive automatic transcoding and subtitle support, ensuring critical information remains accessible even in noisy environments — all while maintaining connections to related items, jobs, and processes.
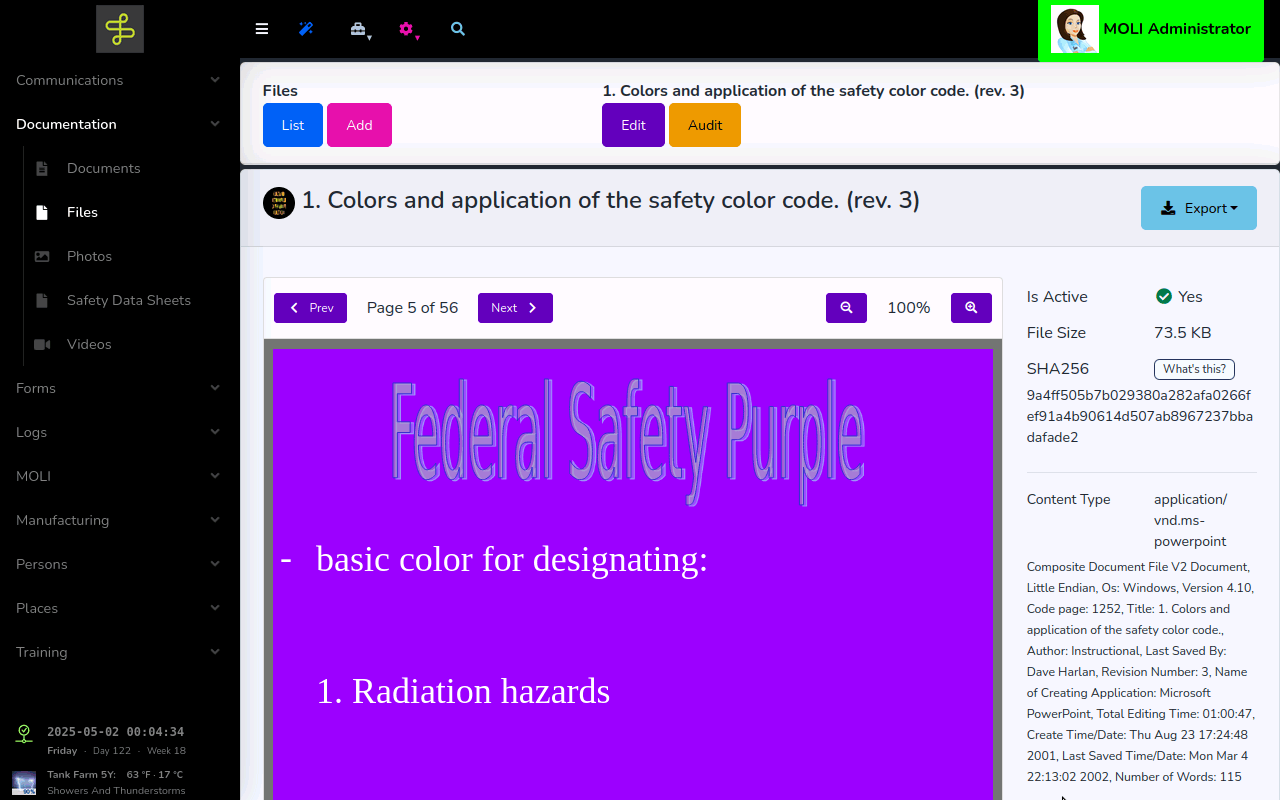
MOLI File Features
- Convert hundreds of different file formats to PDF, including most current and legacy word processing software, spreadsheets, and other documents.
- Work with WordPerfect documents from 1990 as easily as documents you wrote this morning in Microsoft 365.
- Attach an assessment to any uploaded document file, with no need to re-create your instructions in a new format.
- Browse and search all uploaded content, with robust support for common metadata attributes.
- Thumbnail support for thousands of document, video, audio, and manufacturing-specific formats makes it easy to find your content.
- Audio and video subtitle support ensures accessibility, even in loud manufacturing environments
- Automatic video and audio transcoding ensures that video and audio of any format will stream effectively across your intranet.
When it comes to manual data entry, filling out forms is a lot simpler with MOLI — and more accurate.
Since we know what time it is, who you are, and where you are — all we have to ask you for is the data itself. It's impossible to forget to sign your name or record an inaccurate time.
MOLI also supports automatic data collection from a variety of sensors and devices, including scales and moisture analyzers.
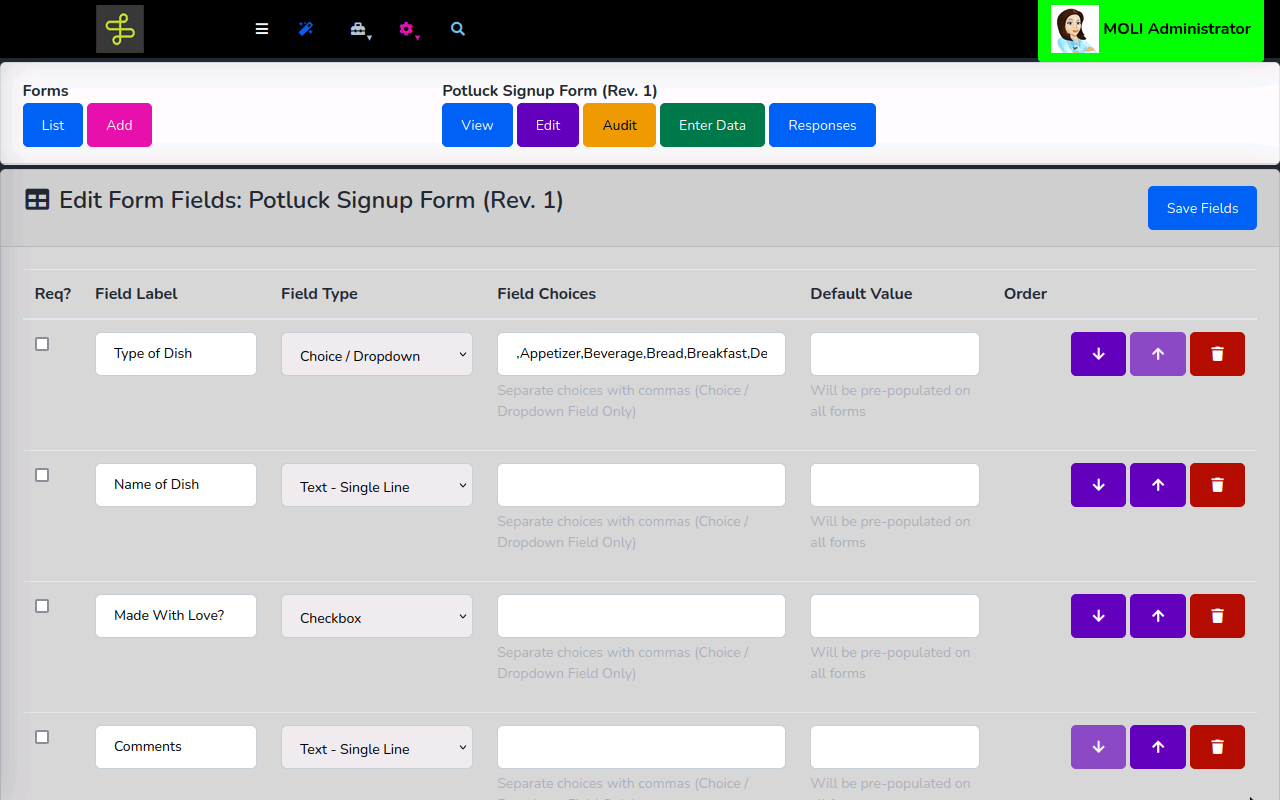
MOLI Forms Features
- Create forms with an unlimited number of custom fields
- Build form fields based on simple field options
- Restrict certain forms to specific Roles
- View and export all form response data
MOLI's Instructions feature transforms complex procedures into role-specific digital guides that display only what each team member needs to see.
The template-driven approach ensures consistent formatting while allowing process-specific customization.
Each instruction can combine text, photos, and videos to clearly communicate proper technique, with automatic tracking of who viewed which version. This targeted information delivery eliminates confusion during complex procedures while creating the controlled document trail required for regulatory compliance.
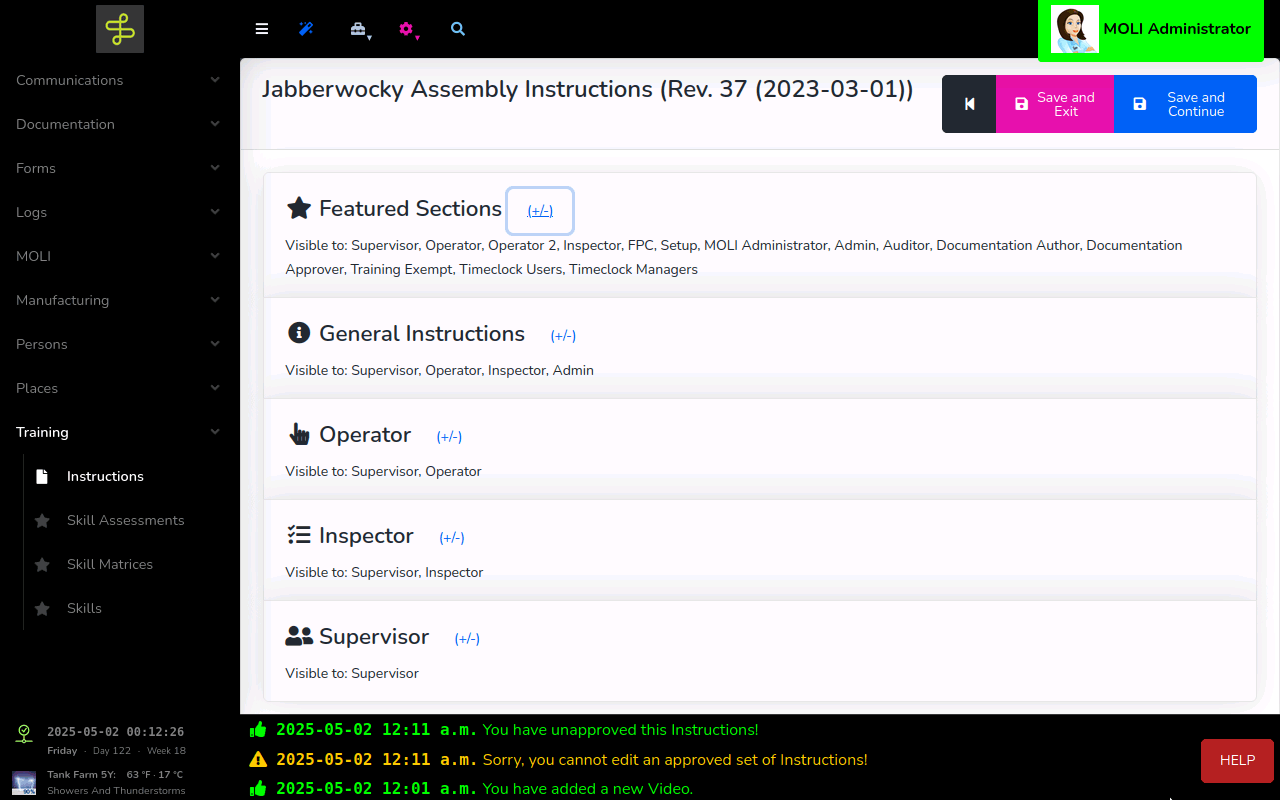
Create a library of photos and other images, then attach them throughout the system.
Incorporate photos into your documentation and browse available metadata.
MOLI's intelligent file processing subsystem preserves accessibility regardless of format or age. The system automatically converts dozens of image file types to standardized formats and generates thumbnails for quick recognition.
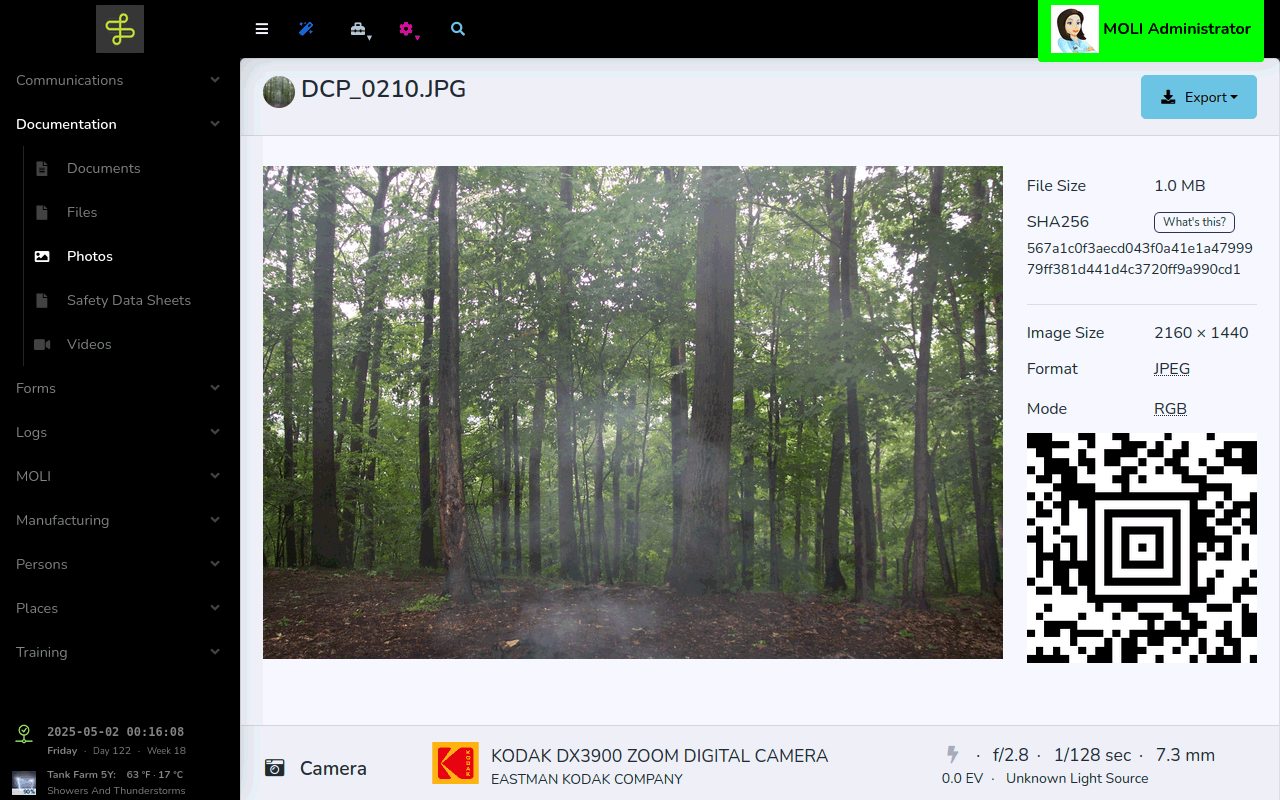
MOLI Photo Features
- Photo Gallery: A centralized hub for your images; search and browse and see connections; attach photos to other things in the system.
- Robust Format Support: Built-in support for generating preview images and thumbnails from hundreds of image file formats, including common web formats (JPG, PNG, WEBP, etc.), legacy formats (LBM, TGA, etc.), and professional formats such as digital negatives and Adobe Photoshop Documents.
- Metadata Support: Full parsing of available image (EXIF) data, including camera information and GPS coordinates.
Upload your SDS to MOLI, creating a collection of documents that can be linked throughout the system.
Safety Data Sheets can be associated with specific Items or Jobs, or simply made available in a simple searchable interface to all personnel.

A full suite of modern software development practices ensure the safety and integrity of the MOLI System.
Each third-party dependency is thoroughly reviewed before inclusion, and is served through private package infrastructure — insulating us from several types of supply chain attack.
A built-in dashboard displays each MOLI deployment's SBOM, allowing for easy verification of system upgrades and software vulnerability mitigations.
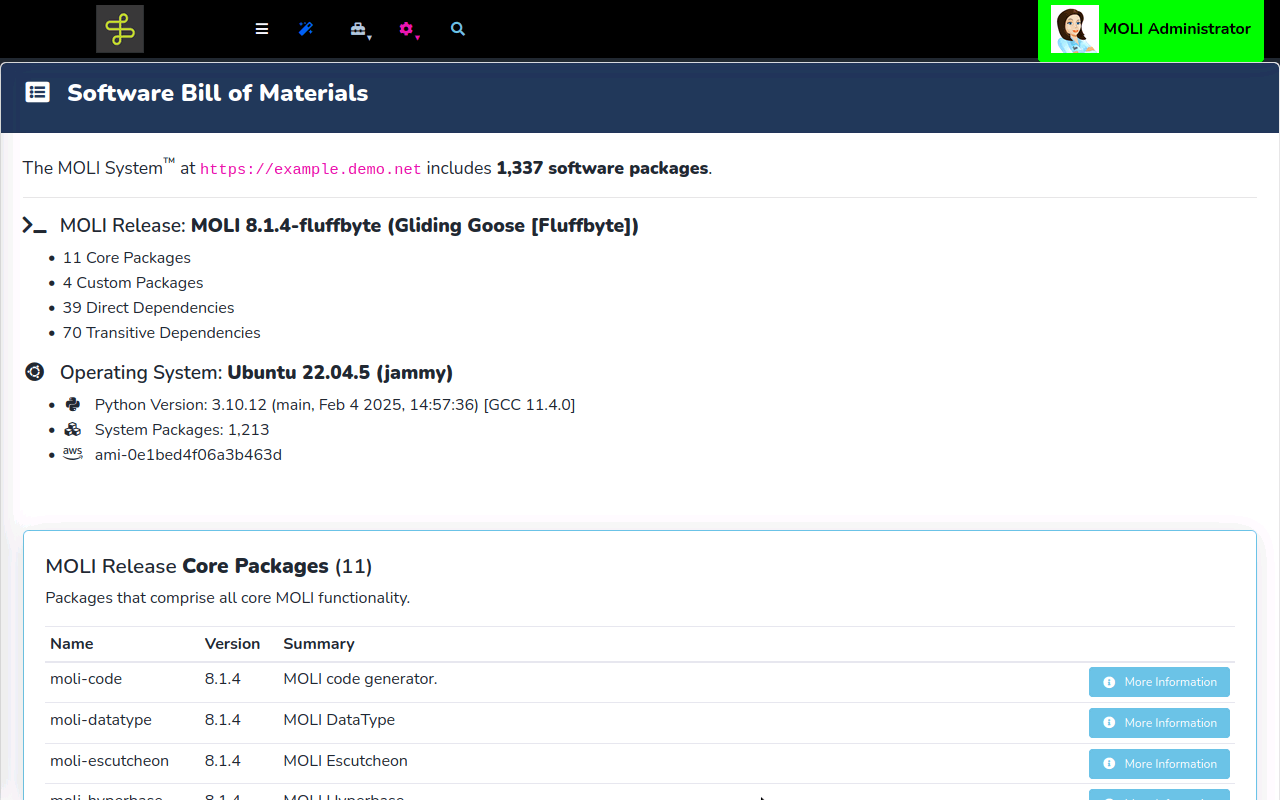
Everything in MOLI can be exported in a wide variety of formats, making your data accessible throughout the enterprise and freeing you from arbitrary format restrictions.
Built-in MOLI Data Export Formats
CSV (Comma Separated Values)
JSON (JavaScript Object Notation)
PDF (Portable Document Format)
PPTX (Microsoft PowerPoint)
TXT (Plain Text)
XLSX (Microsoft Excel)
ZIP (ZIP Archive)
...with more to come!
Create a library of video content that can be used throughout the system to effectively demonstrate processes or concepts.
Videos can be linked to other content or embedded inside of Instructions.
MOLI's intelligent file processing subsystem preserves accessibility regardless of format or age. The system automatically converts hundreds of video file types to streamable formats, generates thumbnails for quick recognition, and handles embedded subtitles.
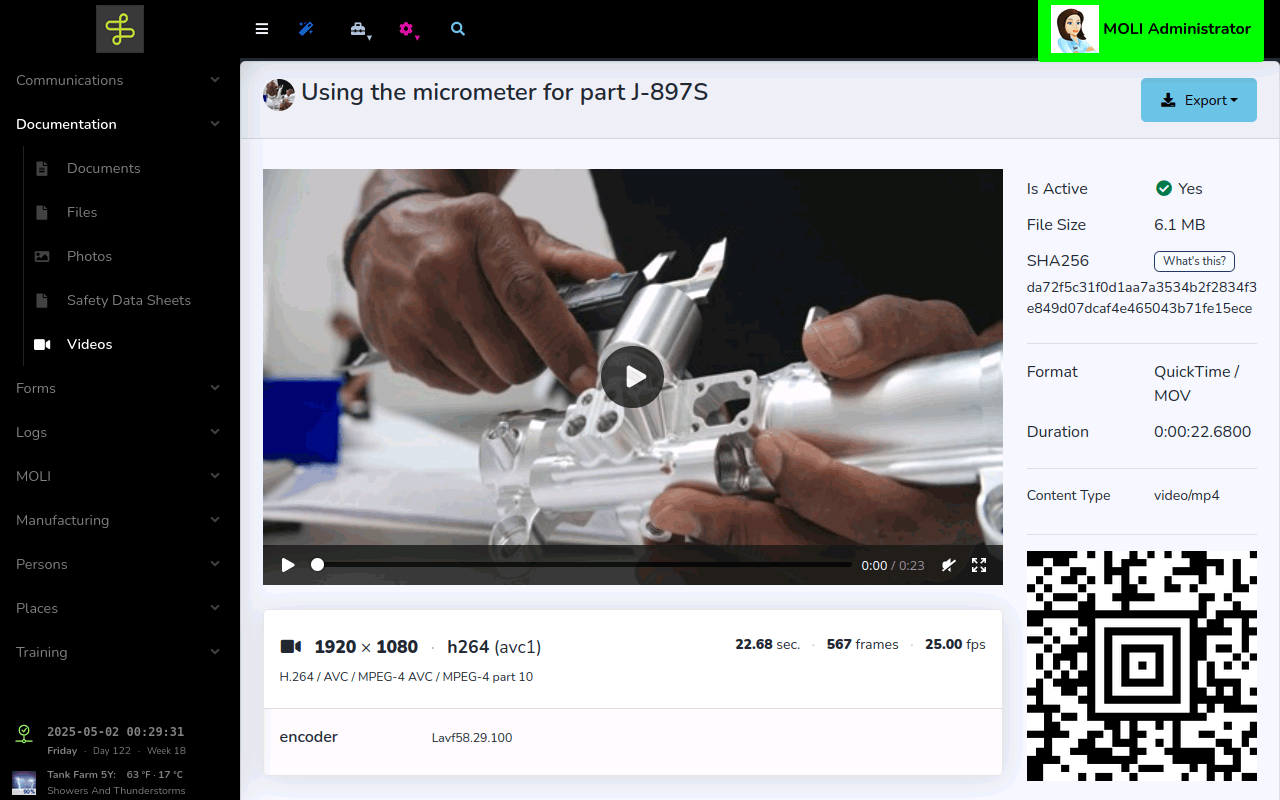
MOLI Video Features
- Include videos in work instructions or documentation to demonstrate key concepts in a dynamic way.
- Attach an assessment to any uploaded video, ensuring that training concepts are understood.
- Browse and search all uploaded content, with robust support for common metadata attributes.
- Thumbnail support for hundreds of video formats makes it easy to find your content.
- Audio and video subtitle support ensures accessibility, even in loud manufacturing environments.
- Automatic video and audio transcoding ensures that video and audio of any format will stream effectively across your intranet.
Key MOLI Features: Manufacturing and Quality Operations…
When it comes to manual data entry, filling out forms is a lot simpler with MOLI — and more accurate.
Since we know what time it is, who you are, and where you are — all we have to ask you for is the data itself. It's impossible to forget to sign your name or record an inaccurate time.
MOLI also supports automatic data collection from a variety of sensors and devices, including scales and moisture analyzers.
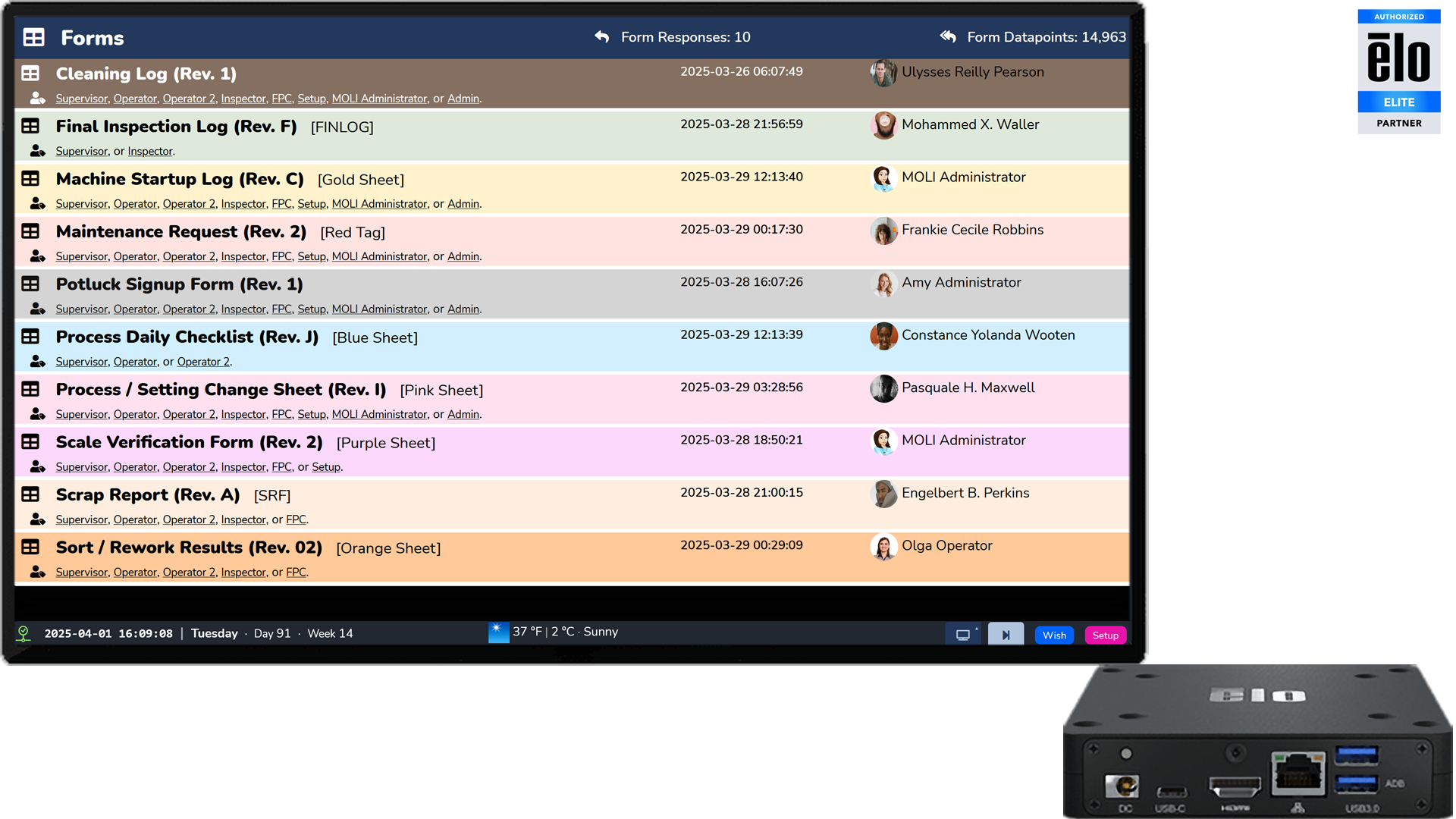
MOLI Forms Features
- Create forms with an unlimited number of custom fields
- Build form fields based on simple field options
- Restrict certain forms to specific Roles
- View and export all form response data
MOLI's Items feature creates comprehensive digital representations of everything you handle — from raw materials to finished products.
Each item profile maintains critical attributes, dimensions, relationships to other items through bill of materials, and links to relevant work instructions and quality forms.
This integrated approach ensures production teams always have accurate specifications at their fingertips while creating traceability connections that satisfy regulatory requirements.
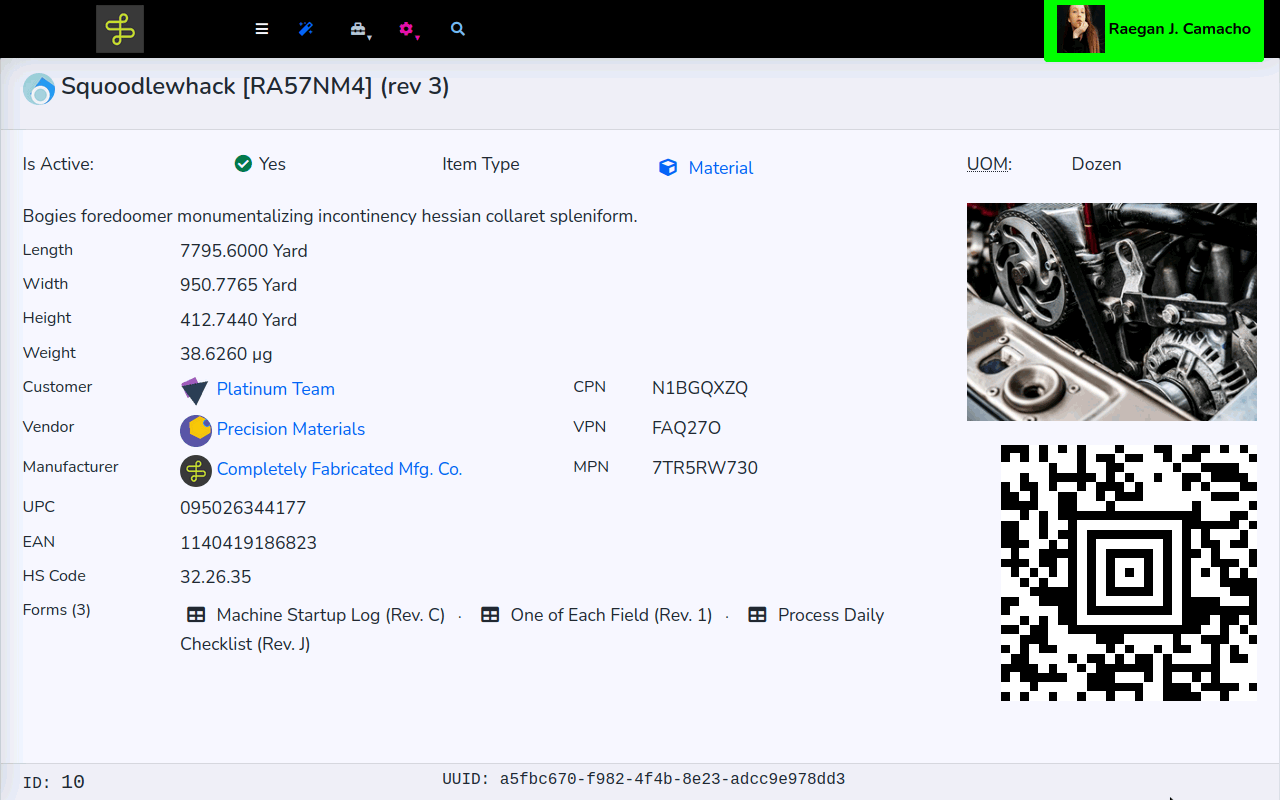
MOLI Item Features
- Basic Attributes including name, code, description, units, photo
- Extended Attributes including dimensions, external codes, and bill of materials
- Create Item-specific work instructions
- Attach forms to items
Easily record good parts and scrapped parts by scrap reason.
Gain valuable insights into fundamental production data, including realtime first-pass yield (FPY) calculations that correlate across all of your key systems.
Job Transactions can be synced back to your ERP system, with built-in and customized integrations available.
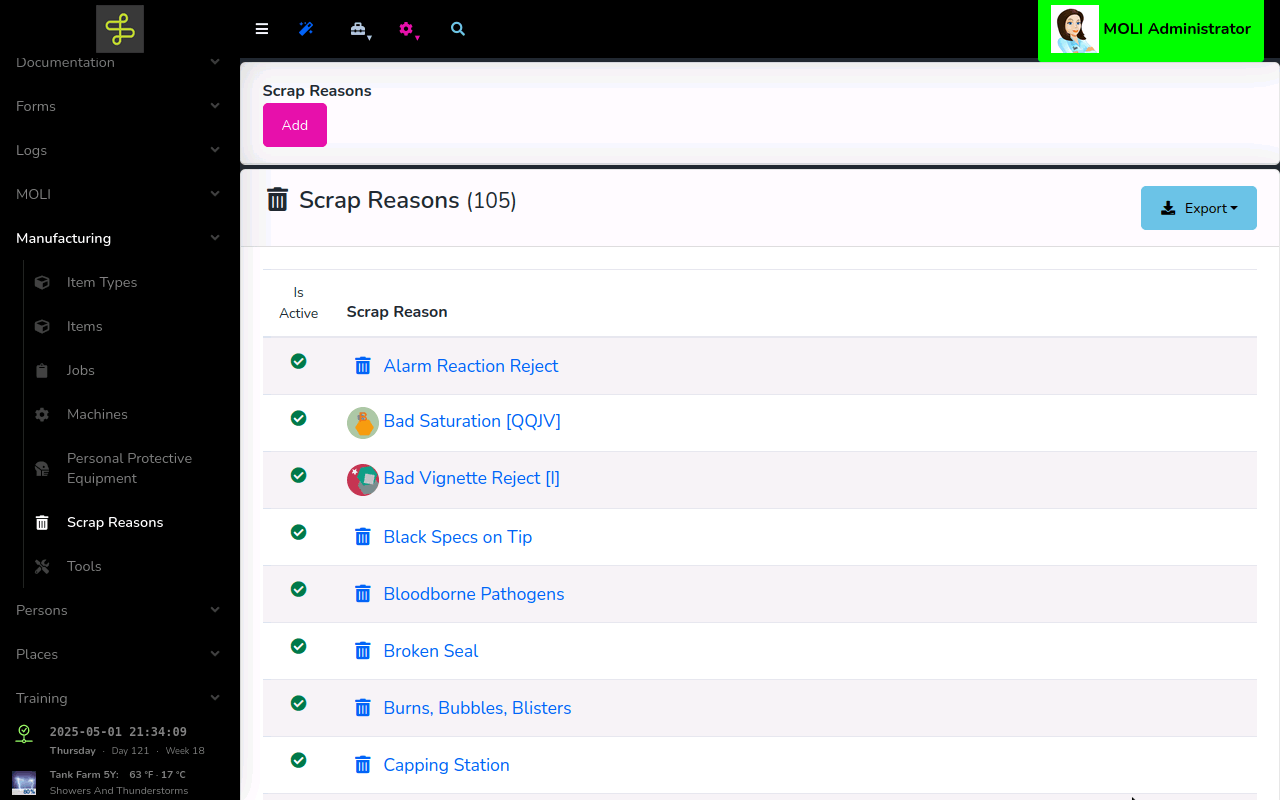
MOLI's Jobs feature creates a digital production pipeline that automatically routes work to appropriate machines and workcenters.
The system integrates directly with popular ERP systems, eliminating manual job creation while ensuring production floor accuracy.
As team members interact with assigned jobs, MOLI dynamically delivers required training, work instructions, and specialized data entry interfaces—creating a paperless workflow that maintains compliance while accelerating production cycles.
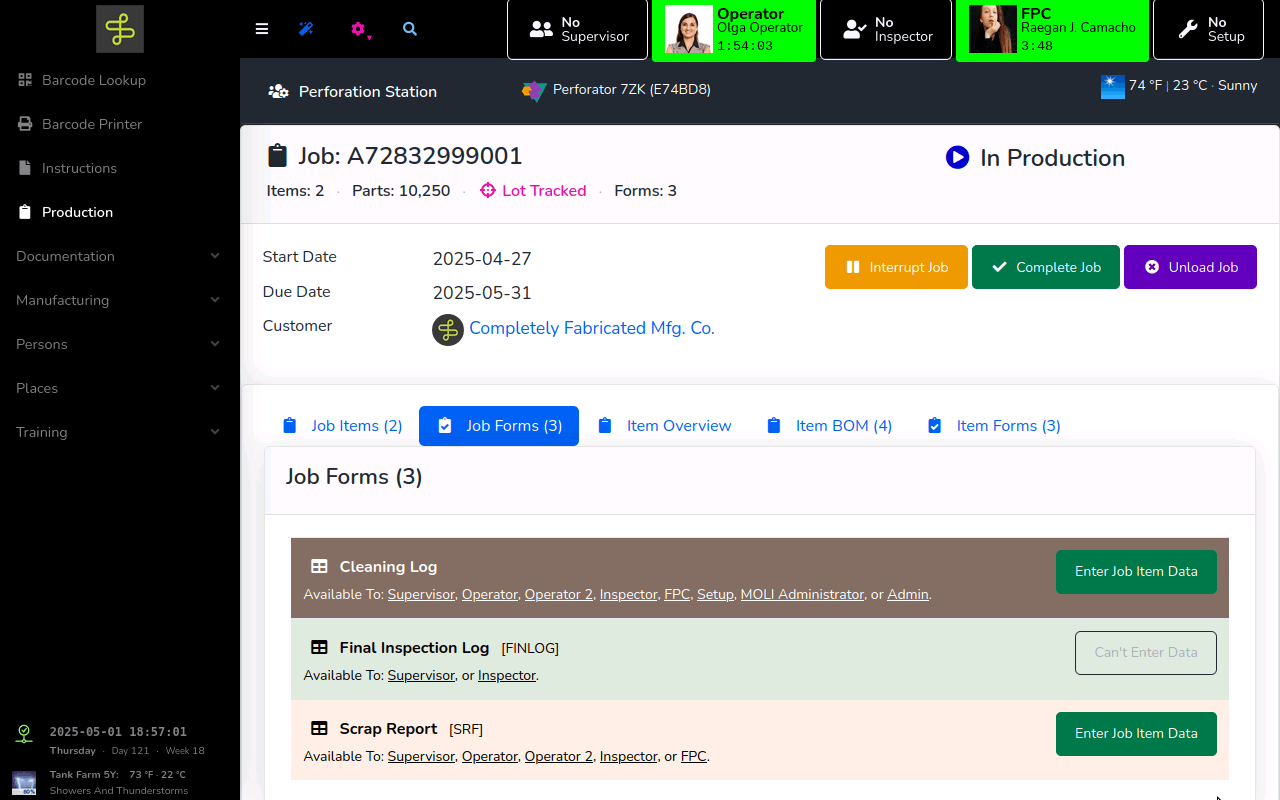
MOLI intelligently routes available jobs to your Machines based on status and completion information.
As employees sign into the job, MOLI delivers required training and assessment — and provides work instructions and data entry interfaces for all job items.
With integrations available for several popular Machine APIs, MOLI helps you unlock the data in your Machines and realize additional value throughout your operation.
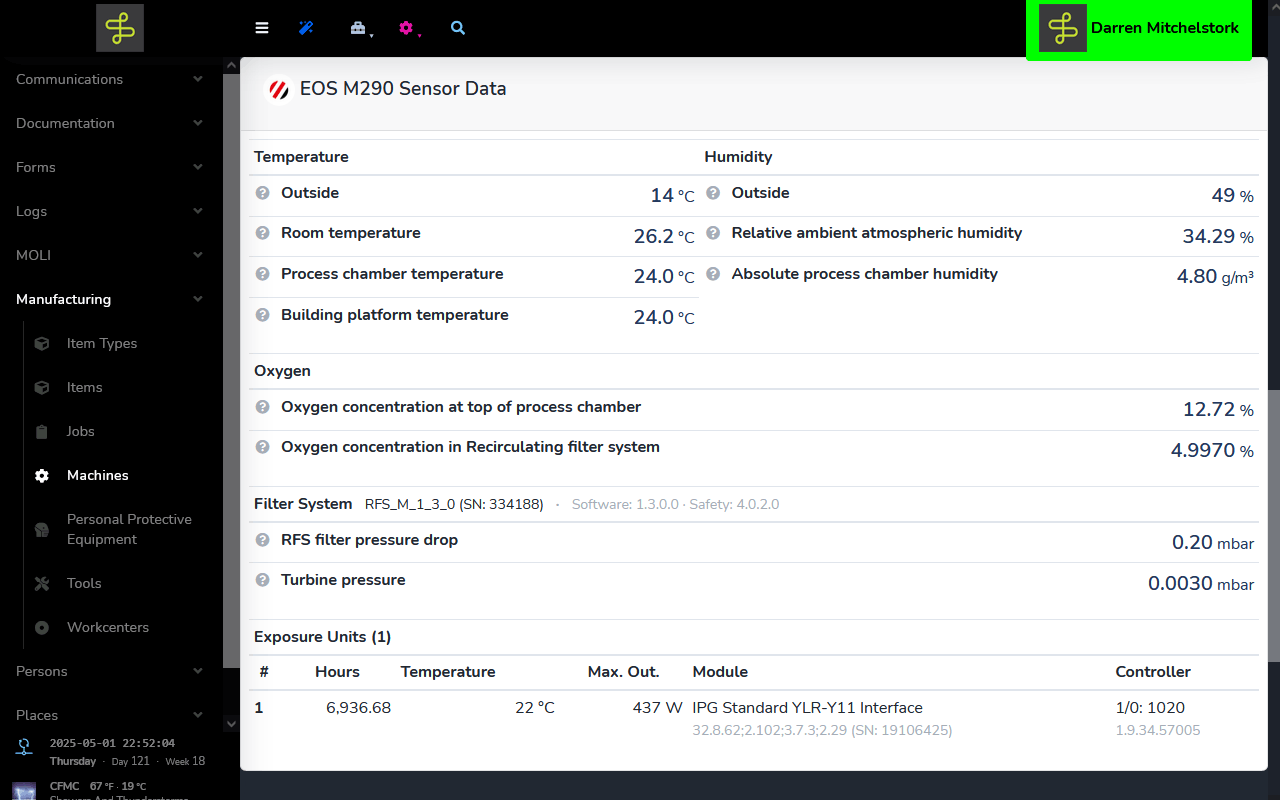
MOLI's Workcenters feature creates digital representations of your production floor's key stations, intelligently routing jobs based on real-time status and capacity.
As team members sign into stations, the system automatically delivers role-specific work instructions, required training materials, and customized data entry interfaces. This contextual delivery ensures processes are followed correctly while capturing critical production data at the source, eliminating paper-based inefficiencies and creating visibility into all aspects of production.
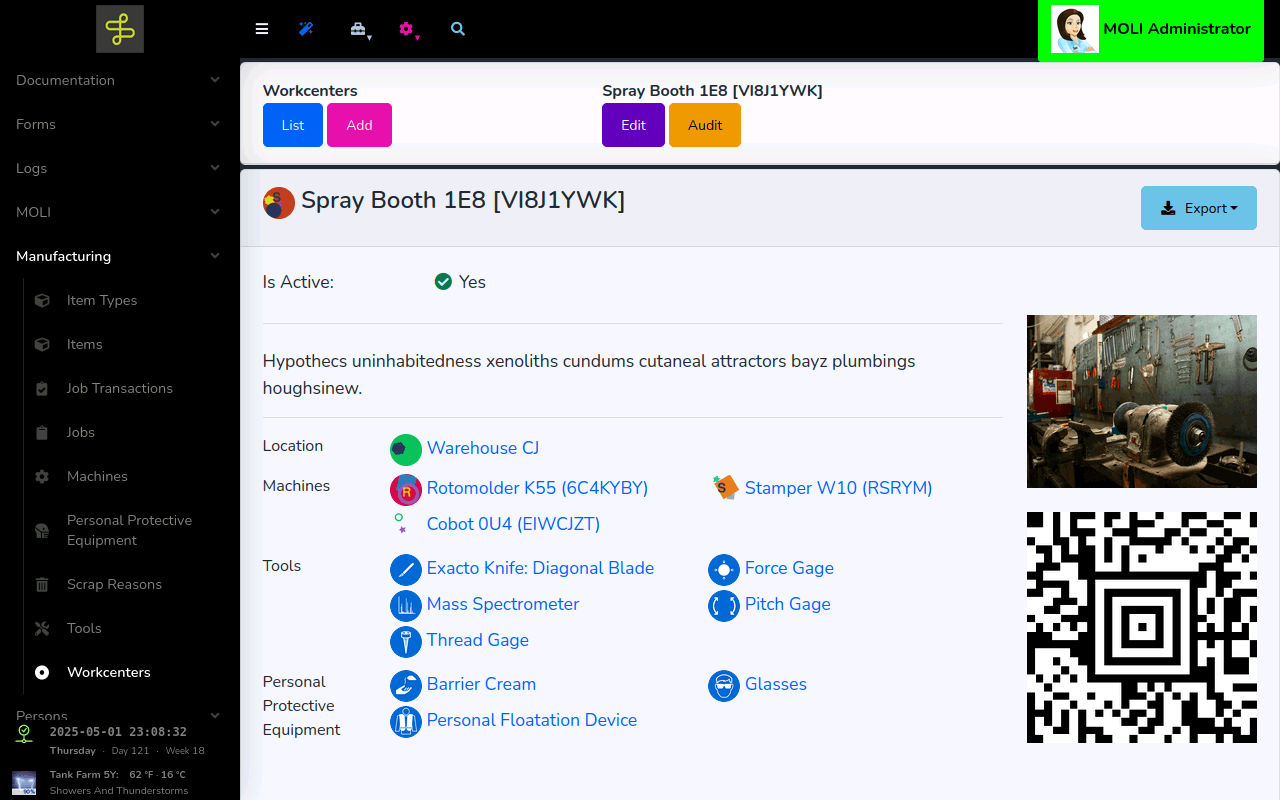
Key MOLI Features: People and Personnel…
MFA makes it more difficult for attackers to gain unauthorized access to your systems.
With robust support for industry-standard two-factor authentication methods, MOLI helps you meet key cybersecurity requirements and keep your data safe.
Additional security factors, such as locations, tokens, physical devices, and the re-authentication workflow, help build further trust in your organization's information security.
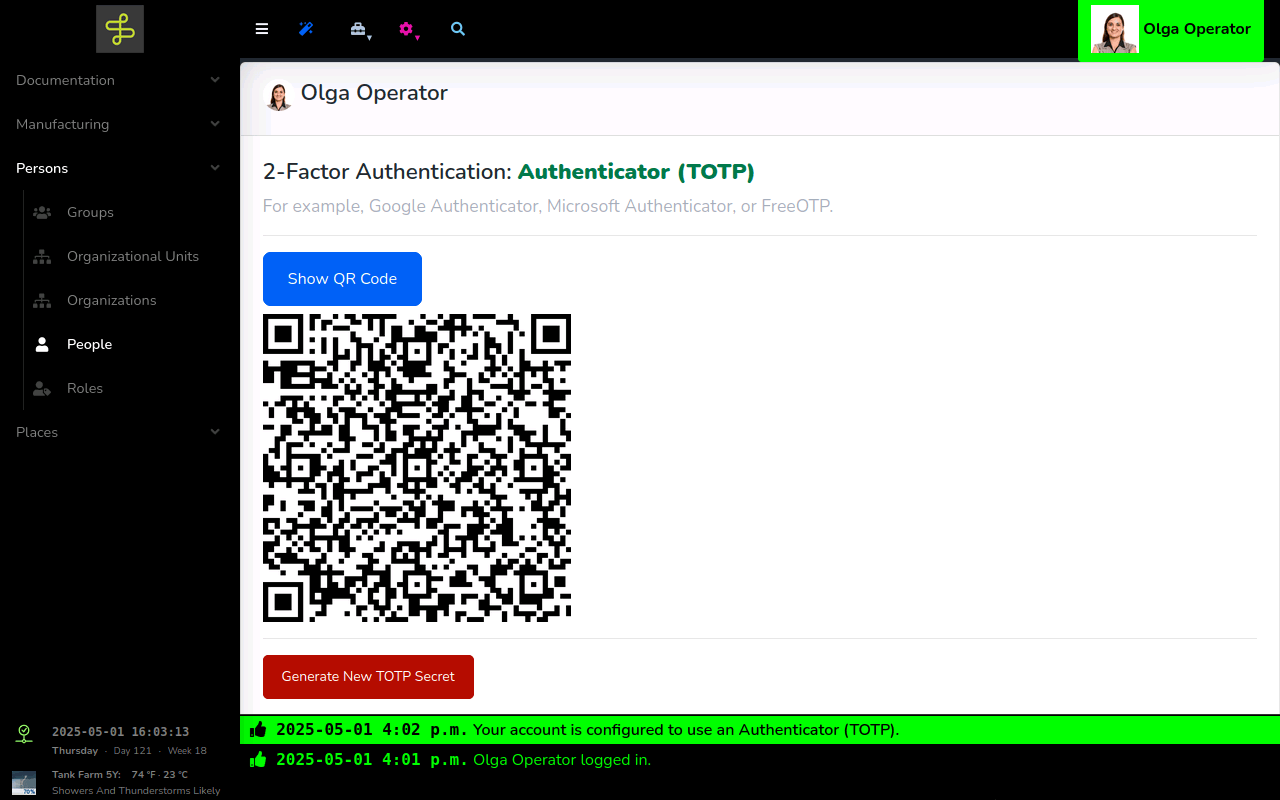
Included MFA Features
- Supported Two-Factor Authentication Methods
- Authenticator App (TOTP) supports Google Authenticator, Microsoft Authenticator, and others.
- Email: MOLI sends you an email containing a code.
- SMS Text Message: MOLI sends you a text message containing a code.
- Voice Call: MOLI calls you on the phone and gives you a code verbally.
- Supported Single-Factor Authentication Methods (for use on secure Kiosk environments)
- Employee ID Number can be used to log in to MOLI Kiosks.
- Employee Barcode can be scanned to grant access to MOLI Kiosks.
- Keyfobs and Keycards with RFID may be used to log in to MOLI Kiosks.
- MOLI Private Cloud adds an additional layer of physical network security to prevent off-site access to the system when Single-Factor Authentication is used.
- Pluggable Re-Authentication Workflow provides additional security for sensitive functions, such as changing the status of a job or crossing out form responses.
MOLI's Organizations feature creates structured profiles for every business entity in your manufacturing ecosystem — from suppliers and customers, to contractors and regulatory bodies.
Each organization connects to relevant items, locations, contacts, and documentation, creating a dynamic map of your supply chain relationships. This centralized approach eliminates scattered contact lists and duplicate records while providing immediate context for communications, quality issues, and compliance documentation.
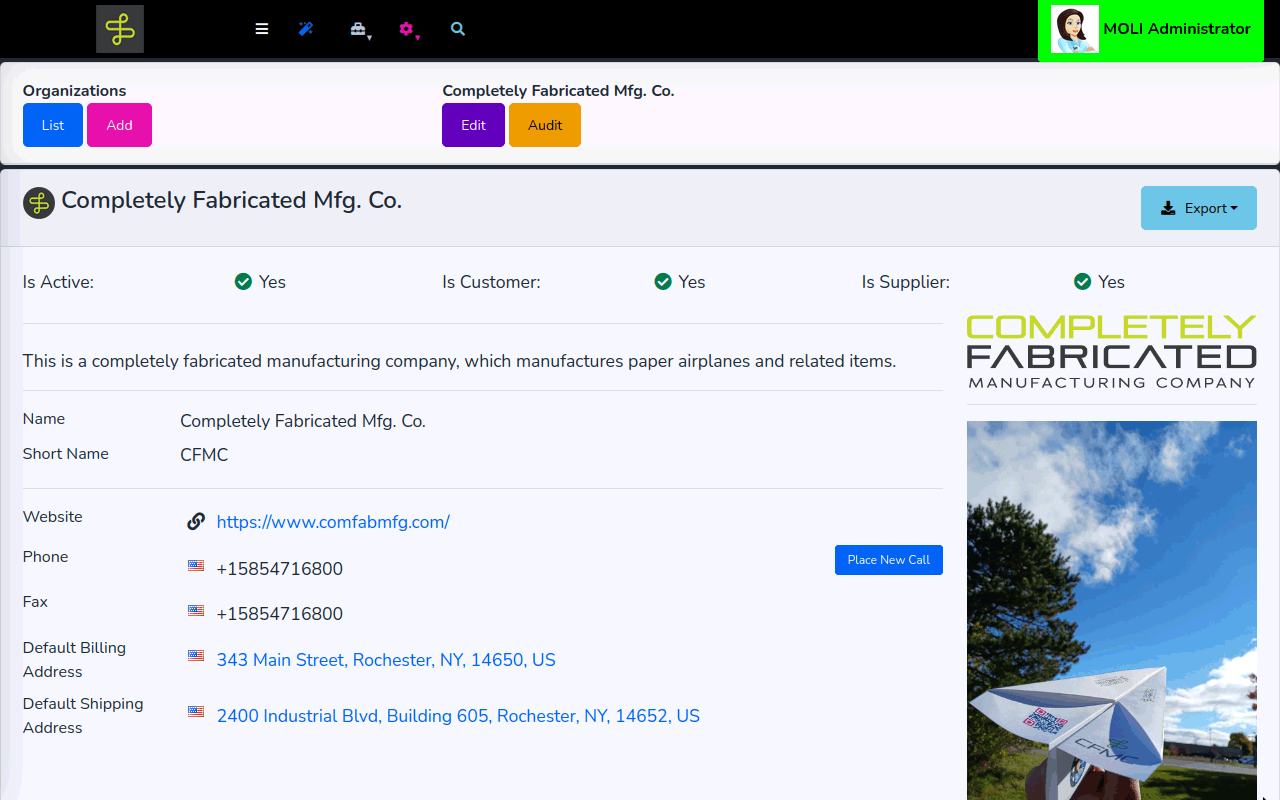
The People feature forms MOLI's human-centered foundation — creating detailed digital profiles for everyone in your manufacturing ecosystem, whether employees, contractors, or external contacts.
Each profile maintains consistent identity information across all MOLI functions and integrations, including multi-part names, photos, organizational relationships, and communication and identification preferences — providing essential context for seamless connections throughout your operation.
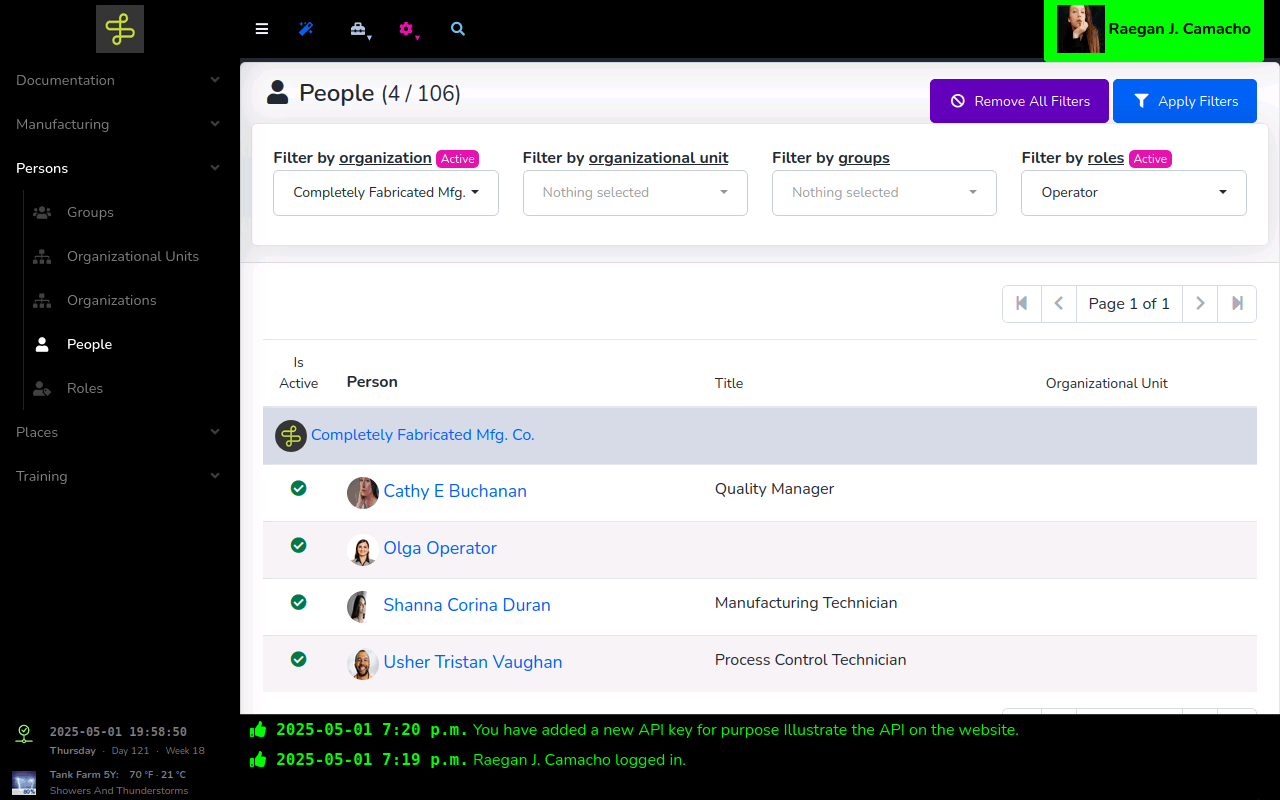
MOLI's Personal API empowers users to create customized JSON-based access to their authorized system data. Each user can generate multiple API keys with granular permission controls, allowing secure integration with external tools and workflows.
The included Bruno™ API Collection download gives developers immediate integration examples tailored to each key's specific permission set, accelerating custom tool development without compromising system security.
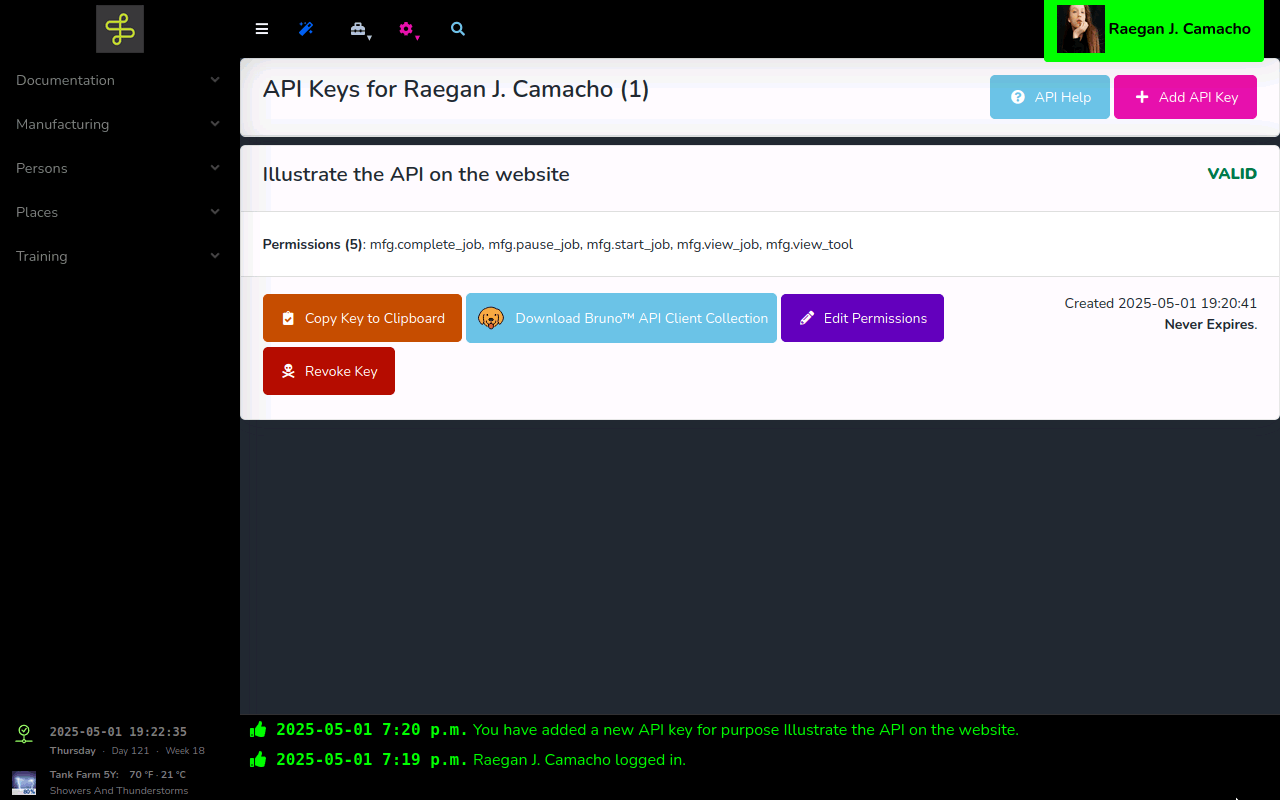
MOLI Roles upgrade traditional permission sets with contextual access controls that govern specific data entry points.
The system's innovative multi-login capability allows multiple roles to be active simultaneously at a single kiosk — enabling operators, inspectors, and supervisors to collaborate efficiently without credential shuffling. This visible role-based approach creates clear accountability while maintaining flexible workflows, letting you see which functional roles are present regardless of which specific team members are on duty.

MOLI's Shifts feature allows you to digitally define your facility's operating schedule by establishing shift patterns and supervisory assignments.
This foundational information enables MOLI to provide critical context throughout the system—displaying the current active shift, directing Escalations to appropriate shift supervisors, and filtering production metrics by shift for accurate performance analysis.
The system adapts to your unique manufacturing schedule, whether you operate standard day shifts or run a complex 24/7 rotation across multiple facilities.

MOLI's Single-Sign-On capability seamlessly integrates with your existing identity management solution (such as Microsoft Entra), allowing team members to access the entire MOLI ecosystem with the same credentials they use for other enterprise systems.
For organizations without an existing identity provider, MOLI can serve as the identity authority itself, extending single-sign-on capabilities to other compatible applications in your environment. This dual-role flexibility ensures MOLI fits naturally into both established enterprise environments and growing operations still building their digital infrastructure.
Built-in MOLI Single-Sign-On (SSO) Features
- Sign-in to MOLI using OpenID Connect (OIDC) authentication, including Microsoft Entra (Azure AD), Okta, and other leading identity providers.
- Utilize MOLI as an OpenID Connect (OIDC) identity provider and log into other systems using your MOLI credentials.
MOLI's integrated Timeclock transforms traditional punch cards into a streamlined digital system that reduces administrative overhead while enhancing accuracy and compliance.
Employees can quickly clock in/out and manage breaks, while management gains real-time visibility into attendance patterns and labor distribution. The system's fraud prevention features and flexible deployment options ensure security and accessibility.
Comprehensive timecard data can be exported to your preferred system or reviewed directly within MOLI, eliminating manual data entry and reconciliation tasks
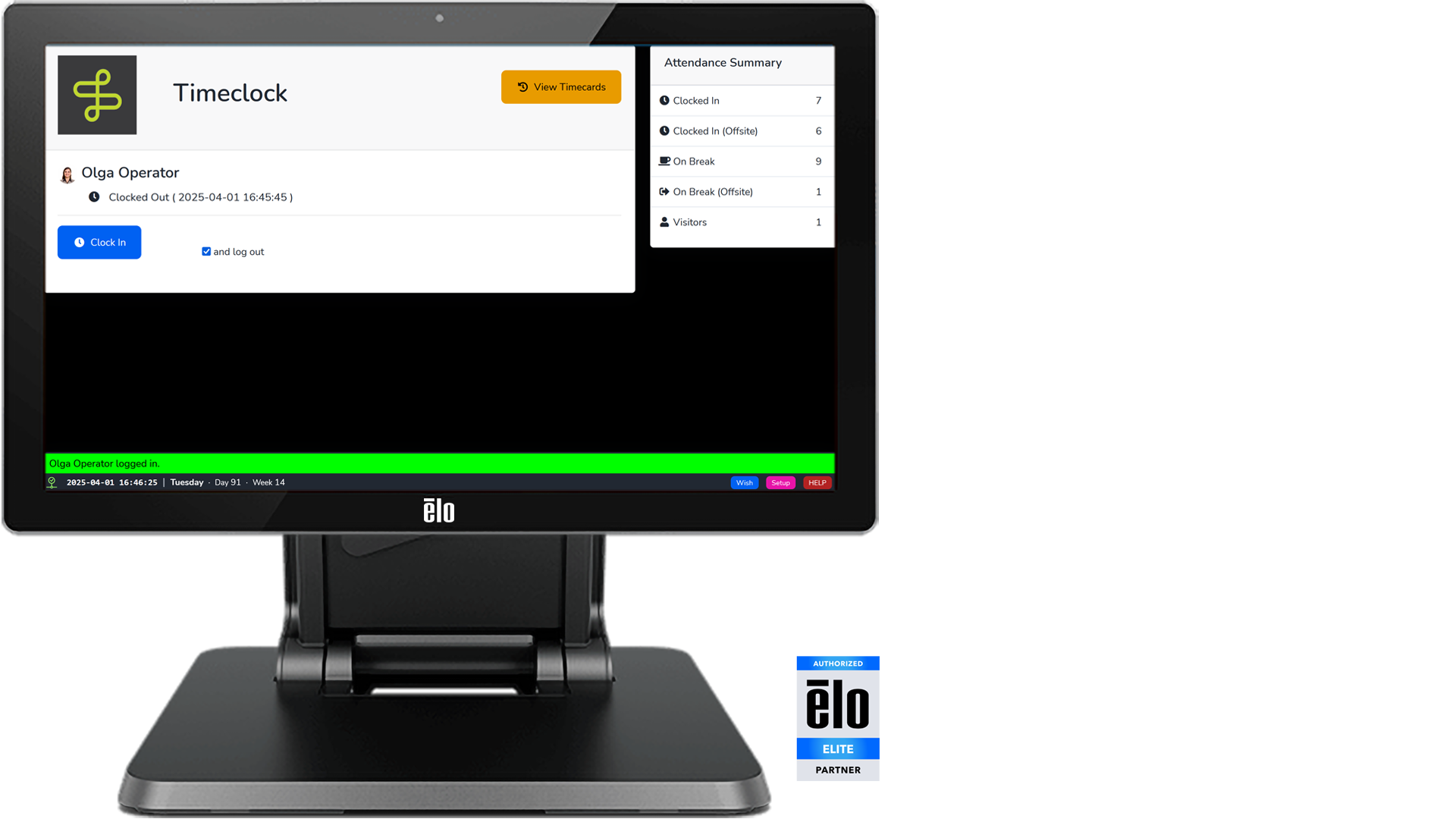
Built-in MOLI Timeclock Features
- Quickly allow employees to clock in, clock out, start breaks, and end breaks.
- Access detailed timecard data and export it to your payroll processor of choice, or simply view it on-screen.
- Snap photos of each time clock event to help prevent timecard fraud.
- Deploy a Timeclock as a dedicated terminal or alongside the Visitor Kiosk or any Production Kiosk
- Integration with Digital Signage to keep you aware of the current headcount and assist with evacuations.
MOLI's integrated Visitor Kiosk transforms your facility entrance into a seamless check-in experience that balances security with hospitality.
Collect essential information, present NDAs for electronic signature, capture visitor photos, and print professional badges—all in one streamlined process. The system automatically notifies appropriate staff of arrivals and maintains comprehensive visitor logs for compliance and security purposes.
By digitizing the entire visitor management workflow, your team can focus on meaningful interactions rather than paperwork, creating a professional first impression that aligns with your operational standards.
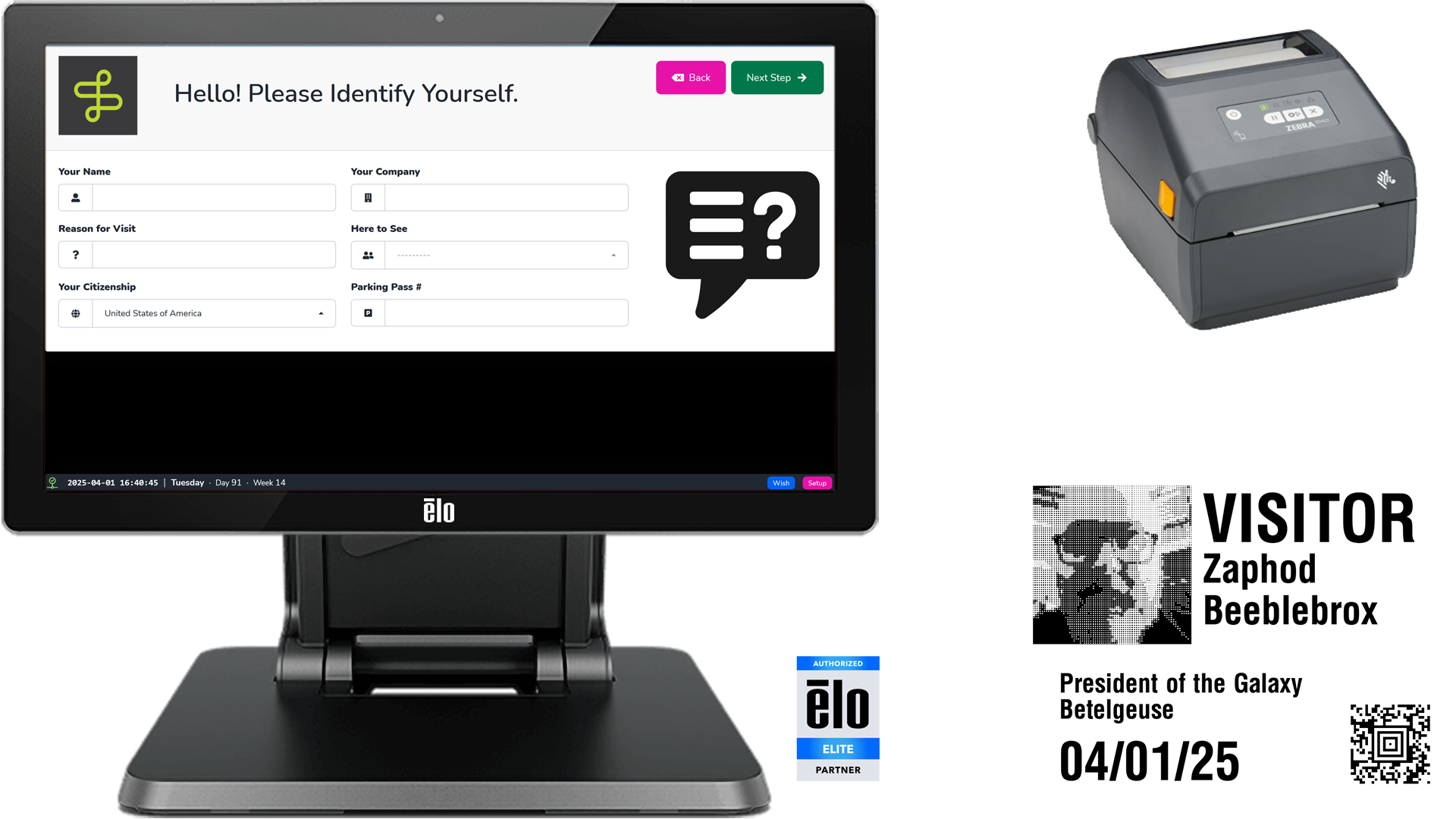
Built-in Visitor Kiosk Features
- Visitor Sign-In Quesionnaire: Ask each visitor for the purpose of their visit, who they're here to see, their citizenship, their parking pass number, or any other required information.
- Non-Disclosure Agreement: Present your NDA at sign-in time and collect signatures from your visitors. Review signatures later to ensure compliance with your policies.
- Host Notification: Configurable email, voice call, SMS, and overhead voice paging notifications of visitor arrival.
- Take Photos / Snap Pictures: Invite each visitor to pose for an official photo and / or simply snap their picture when they sign in.
- Well-designed Visitor Badges printed with or without photos.
- Integration with Digital Signage to make your staff aware of visitors and assist with evacuations.
- Visitor Sign-Out using barcode printed on visitor badge, or manually.
Software systems work best when they can talk to each other.
MOLI integrations leverage a common integration framework, which ensures rapid, high quality development and future maintainability.
Key MOLI Features: Software and Machine Integrations…
By leveraging installed MQTT and REST API modules, MOLI can communicate with Arburg ALS.
MOLI can mirror each machine's status, trigger actions based on machine status, and help bridge the gaps between automatic machine part counts, manual operator part counts, and ERP system job transactions.
MOLI's EOSCONNECT integration unifies your EOS DMLS 3D printers, transforming isolated machines into networked production assets.
By leveraging the machine's native API, MOLI displays real-time build status across your facility, triggers automated workflows based on print completion or failures, and routes critical notifications to appropriate personnel.
This connection eliminates manual monitoring, reduces response times to machine issues, and provides valuable production data for analysis — without requiring operators to physically check each printer or export data manually.
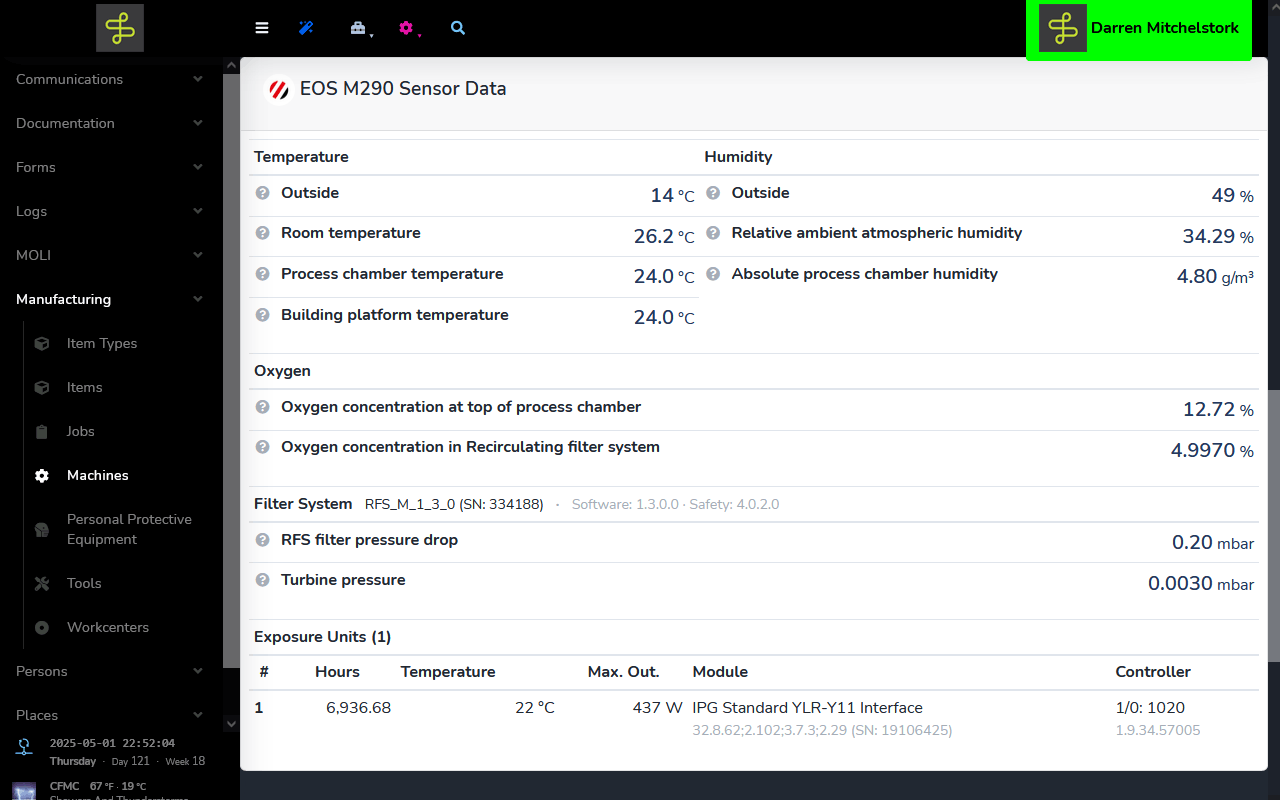
MOLI's SyteLine integration creates a bidirectional connection with your on-premises ERP system, automatically synchronizing critical production data. Jobs entered in SyteLine appear in MOLI, while completed production activities in MOLI generate unposted Job Transactions ready for approval in SyteLine.
This seamless data flow eliminates manual re-entry, reduces transcription errors, and provides real-time visibility to production status across both systems without disrupting existing approval workflows.
MOLI's Local Network Fileshare feature automatically exports and synchronizes critical information to your local network drives. As data changes within MOLI—whether job statuses, production metrics, or quality reports—the corresponding export files update in real-time, enabling legacy applications to access current information without manual exports.
This automatic synchronization eliminates duplicate data entry while letting you leverage existing software investments alongside MOLI's advanced capabilities.
MOLI's Business Central integration creates a bidirectional connection with your cloud-based ERP system, automatically synchronizing critical production data. Production Orders entered in Business Central appear in MOLI, while completed production activities in MOLI can generate unposted Journal Entries ready for approval in Business Central.
This seamless data flow eliminates manual re-entry, reduces transcription errors, and provides real-time visibility to production status across both systems without disrupting existing approval workflows.
MOLI's eFileCabinet integration creates a unidirectional connection with your on-premises documentation system, automatically creating a record of production activity.
As data changes within MOLI—whether job statuses, production metrics, or quality reports—the corresponding export files update in real-time, and are synced to their configured eFC drawer.
This seamless data flow eliminates manual re-entry and ensures that your records are complete.
MOLI ensures all staff receive required work instructions, and provides evidence of training with a full graded assessment, simple verification process, or personal skill assessment as needed.
Key MOLI Features: Training and Assessment…
MOLI's Assessments feature provides automated proof of training through customizable digital quizzes that verify knowledge retention.
Multiple question formats, flexible scoring strategies, and configurable passing thresholds let you tailor evaluations to specific processes or regulatory requirements.
Failed assessments trigger optional supervisor intervention workflows, creating accountable resolution paths while successful completions generate permanent training records for compliance documentation.
MOLI's Instructions feature transforms complex procedures into role-specific digital guides that display only what each team member needs to see.
The template-driven approach ensures consistent formatting while allowing process-specific customization.
Each instruction can combine text, photos, and videos to clearly communicate proper technique, with automatic tracking of who viewed which version. This targeted information delivery eliminates confusion during complex procedures while creating the controlled document trail required for regulatory compliance.
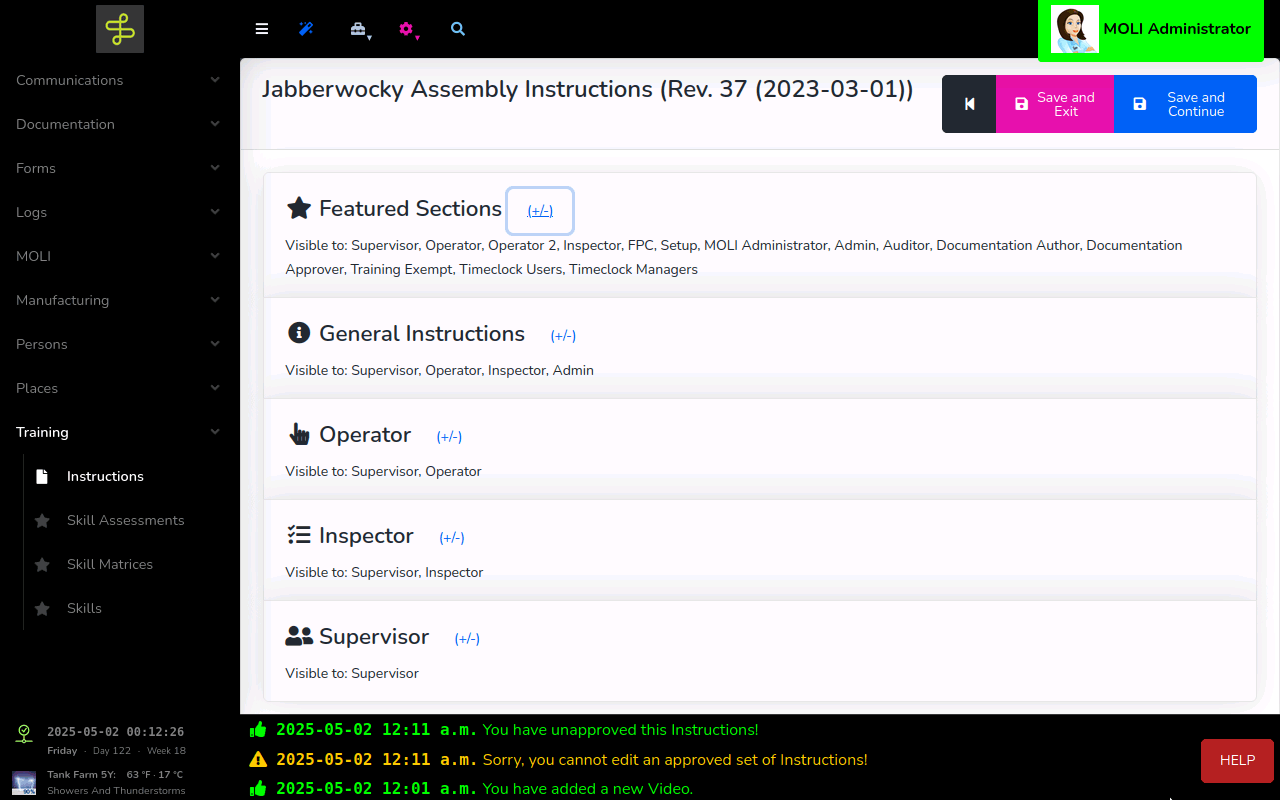
MOLI's Skill Matrix creates a visual competency dashboard connecting your team's abilities to production requirements.
The system enables supervised skill validation through structured assessments, with supervisors confirming proficiency levels during actual work observation.
This real-time capability tracking ensures critical operations maintain proper coverage during absences, identifies training needs before they impact quality, and provides immediate verification of compliance with regulatory skill requirements.
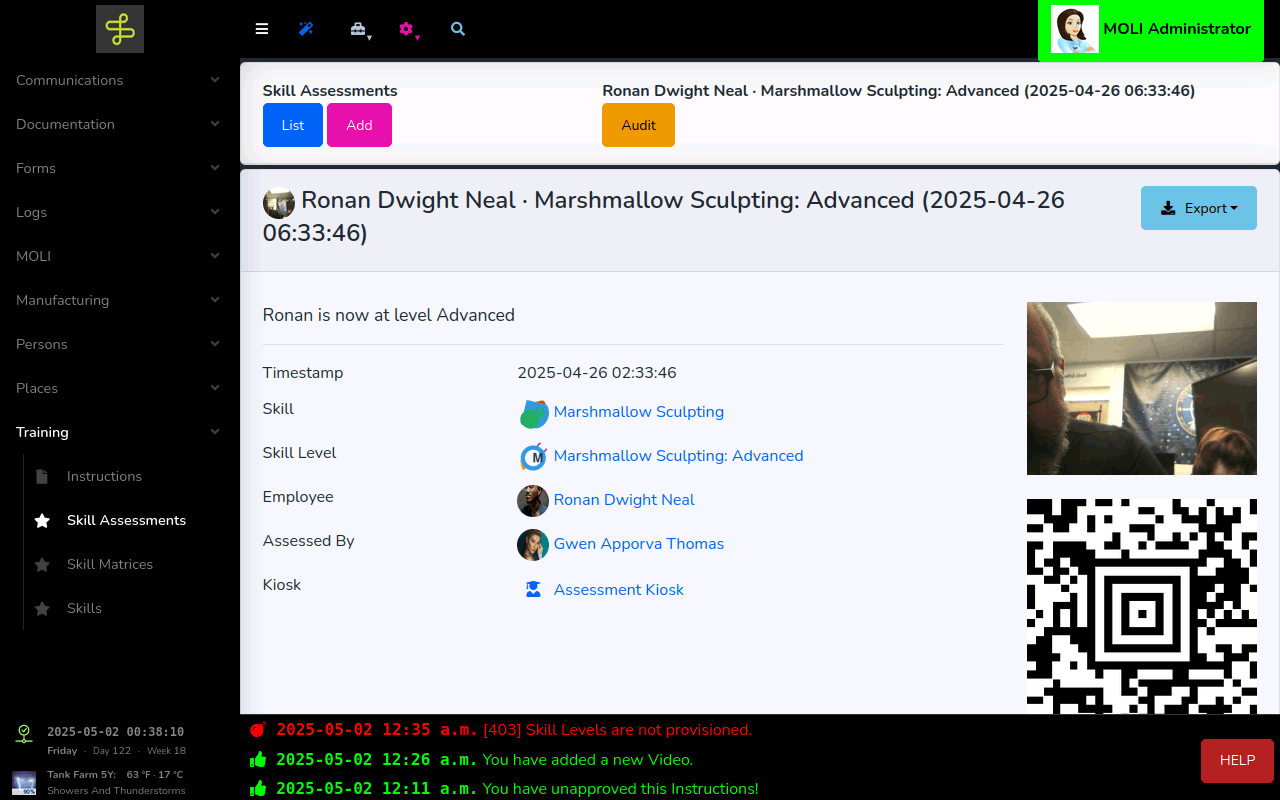
MOLI's Training Transcript provides a comprehensive digital record of all learning activities across your organization, capturing assessment scores, skill validations, and verification completions in one searchable interface.
This centralized training history enables rapid compliance verification during audits, identifies team members with specialized knowledge, and highlights training gaps before they impact production quality.
The system automatically maintains these records as training occurs, eliminating manual documentation while providing immediate visibility to training status.
MOLI's Training Verification documents when team members receive critical instructions and captures supervisor certification of competence.
This digital record creates defensible evidence of proper training for ISO 9001 and ISO 13485 compliance audits, replacing manual sign-off sheets with timestamps, electronic signatures, and links to the exact instructions provided.
The streamlined process ensures consistent verification without administrative burden, creating a training accountability system that satisfies both operational needs and regulatory requirements